Article Navigation
- Introduction: Navigating the Global Market for Sensory Training Equipment for Pediatric Occupational Therapy Clinic Kids Hospital
- Understanding Sensory Training Equipment for Pediatric Occupational Therapy Clinic Kids Hospital Types and Variations
- Key Industrial Applications of Sensory Training Equipment for Pediatric Occupational Therapy Clinic Kids Hospital
- Strategic Material Selection Guide for Sensory Training Equipment for Pediatric Occupational Therapy Clinic Kids Hospital
- In-depth Look: Manufacturing Processes and Quality Assurance for Sensory Training Equipment for Pediatric Occupational Therapy Clinic Kids Hospital
- Comprehensive Cost and Pricing Analysis for Sensory Training Equipment for Pediatric Occupational Therapy Clinic Kids Hospital Sourcing
- Spotlight on Potential Sensory Training Equipment for Pediatric Occupational Therapy Clinic Kids Hospital Manufacturers and Suppliers
- Essential Technical Properties and Trade Terminology for Sensory Training Equipment for Pediatric Occupational Therapy Clinic Kids Hospital
- Navigating Market Dynamics, Sourcing Trends, and Sustainability in the Sensory Training Equipment for Pediatric Occupational Therapy Clinic Kids Hospital Sector
- Frequently Asked Questions (FAQs) for B2B Buyers of Sensory Training Equipment for Pediatric Occupational Therapy Clinic Kids Hospital
- Important Disclaimer & Terms of Use
- Strategic Sourcing Conclusion and Outlook for Sensory Training Equipment for Pediatric Occupational Therapy Clinic Kids Hospital
Introduction: Navigating the Global Market for Sensory Training Equipment for Pediatric Occupational Therapy Clinic Kids Hospital
Sensory training equipment plays a pivotal role in pediatric occupational therapy, providing essential tools that support the developmental and therapeutic needs of children in clinics and hospital settings. For healthcare providers and institutional buyers worldwide, sourcing the right sensory equipment is critical to enhancing therapy outcomes, improving patient engagement, and ensuring safety and compliance. This guide is tailored to empower international B2B buyers, especially those operating in diverse markets such as Africa, South America, the Middle East, and Europe, including regions like South Africa and Australia.
Understanding the global landscape of sensory training equipment requires insight into various product categories—from sensory gym installations and tactile toys to weighted blankets and interactive sensory walls. Beyond types, this guide covers material quality, manufacturing standards, and rigorous quality control processes that ensure durability and safety. It also provides an in-depth analysis of trusted suppliers, cost structures, and market trends specific to pediatric occupational therapy.
By navigating this comprehensive resource, buyers will gain actionable knowledge to make informed procurement decisions that align with clinical objectives, budget constraints, and regional regulatory requirements. Whether upgrading existing facilities or establishing new therapy centers, this guide offers a strategic framework for sourcing sensory training equipment that meets the highest therapeutic standards while addressing the unique demands of international markets.
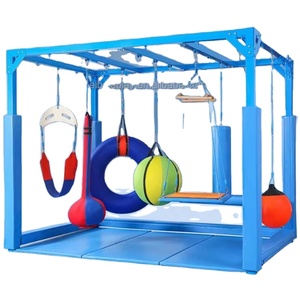
Illustrative Image (Source: Google Search)
Understanding Sensory Training Equipment for Pediatric Occupational Therapy Clinic Kids Hospital Types and Variations
Type Name | Key Distinguishing Features | Primary B2B Applications | Brief Pros & Cons for Buyers |
---|---|---|---|
Sensory Gym Equipment | Multi-sensory integration tools such as swings, trampolines, and obstacle courses | Pediatric clinics, hospitals, therapy centers | Pros: Versatile, improves gross motor and sensory skills; Cons: Requires space, supervision needed |
Sensory Room Equipment | Specialized lighting (fiber optic, bubble tubes), tactile panels, interactive floor projectors | Kids hospitals, pediatric OT clinics, special schools | Pros: Calming, customizable; Cons: Higher initial investment, installation complexity |
Weighted and Soft Toys | Weighted blankets, stuffed animals, sensory pillows, fidget toys | Occupational therapy clinics, home use, schools | Pros: Portable, cost-effective; Cons: Limited gross motor engagement, hygiene considerations |
Sensory Interactive Tools | Touch-sensitive panels, interactive mats, LED furniture, and floor tiles | Therapy centers, schools, pediatric hospitals | Pros: Engaging, tech-enabled; Cons: Higher cost, maintenance requirements |
Fine Motor Skill Tools | Therapy putty, busy boards, magnetic mazes, STEM building toys | Pediatric OT clinics, educational institutions | Pros: Enhances fine motor skills and cognitive development; Cons: May require frequent replacement |
Sensory Gym Equipment incorporates dynamic tools like trampolines, swings, and obstacle courses designed to engage children’s vestibular and proprioceptive senses. These equipment types are ideal for pediatric occupational therapy clinics and hospitals aiming to improve gross motor skills alongside sensory processing. B2B buyers should consider facility space, safety standards, and the need for trained staff to maximize therapeutic outcomes. Bulk procurement may reduce costs, but installation and supervision are critical factors.
Sensory Room Equipment features specialized sensory lighting (fiber optic lights, bubble tubes), tactile walls, and interactive sensory stations that create immersive environments. These are well-suited for pediatric hospitals and clinics focusing on sensory modulation and calming therapies. Buyers should evaluate power requirements, room customization options, and durability. Although initial costs and installation complexity are higher, these rooms offer long-term therapeutic benefits and can be a differentiator in high-end pediatric care centers.
Weighted and Soft Toys such as weighted blankets, sensory pillows, and fidget toys provide tactile and proprioceptive input in a portable form. These are popular for clinics with limited space or for home-based therapy programs. B2B buyers benefit from their affordability and ease of use but must ensure hygienic materials and ease of cleaning for repeated use in clinical settings. These items complement larger equipment by supporting self-regulation and calming.
Sensory Interactive Tools include touch-sensitive wall panels, LED-lit furniture, and interactive floor projectors that engage children through technology-enhanced sensory experiences. These tools are particularly effective in modern pediatric hospitals and therapy centers embracing digital integration. Buyers should assess the total cost of ownership, including maintenance and software updates, and consider training requirements for staff. Their high engagement potential justifies investment for clinics targeting tech-savvy patient populations.
Fine Motor Skill Tools focus on activities to develop hand-eye coordination and dexterity, such as therapy putty, busy boards, and STEM building toys. These are essential in pediatric occupational therapy clinics and educational settings aiming to enhance cognitive and motor skill development. B2B buyers should consider product durability and replacement cycles, as well as age-appropriateness for diverse patient groups. Bundling these tools with sensory equipment can provide comprehensive therapy solutions.
Related Video: Sensory Integration Therapy – Pediatric Occupational Therapy
Key Industrial Applications of Sensory Training Equipment for Pediatric Occupational Therapy Clinic Kids Hospital
Industry/Sector | Specific Application of Sensory Training Equipment for Pediatric Occupational Therapy Clinic Kids Hospital | Value/Benefit for the Business | Key Sourcing Considerations for this Application |
---|---|---|---|
Pediatric Healthcare Facilities | Integration of sensory gym equipment (e.g., weighted vests, swings, tactile toys) for developmental therapy | Enhances patient outcomes by improving sensory processing and motor skills | Equipment safety certifications, durability, ease of cleaning, and multi-sensory features |
Educational Institutions (Special Needs Schools) | Use of sensory rooms and interactive sensory toys to support children with sensory processing disorders | Supports inclusive education, improves student engagement and learning outcomes | Compliance with educational standards, adaptability to classroom environments, and modularity |
Rehabilitation Centers | Deployment of obstacle courses and fine motor skill tools to aid recovery and skill development | Accelerates rehabilitation progress and increases therapy session effectiveness | Robustness for frequent use, portability, and customization options for therapy goals |
Pediatric Research Institutes | Use of sensory training tools for clinical trials and developmental studies on sensory integration | Facilitates data collection and innovative therapy method development | Precision of equipment, data integration capabilities, and supplier reliability |
Home Healthcare Providers | Provision of compact sensory kits and weighted blankets for at-home therapy and parental guidance | Expands therapy reach, enhances continuity of care, and improves family involvement | Portability, ease of use, and clear instructional support for caregivers |
Pediatric Healthcare Facilities
In pediatric hospitals and clinics, sensory training equipment such as weighted vests, swings, and tactile toys are essential for occupational therapists to address sensory processing challenges and improve motor coordination. These tools help children with neurological or developmental disorders engage in sensory integration therapy, promoting better self-regulation and functional independence. For international B2B buyers, especially in Africa and South America, sourcing equipment that meets stringent safety standards and offers durability in diverse climatic conditions is crucial to ensure long-term usability and patient safety.
Educational Institutions (Special Needs Schools)
Special needs schools rely heavily on sensory rooms equipped with interactive toys, fiber optic lights, and sensory mats to create stimulating environments tailored to children with sensory processing disorders. These applications help improve attention, reduce anxiety, and facilitate learning through multi-sensory engagement. Buyers from the Middle East and Europe should prioritize equipment that complies with local educational regulations, is easy to integrate into existing classrooms, and offers flexibility to accommodate various student needs and developmental stages.
Rehabilitation Centers
Rehabilitation centers use obstacle courses, trampolines, and fine motor skill tools to support children recovering from injuries or developmental delays. These equipment pieces enable therapists to work on muscle strength, coordination, and motor planning in a controlled, engaging setting. For B2B buyers in regions like South Africa and Australia, sourcing equipment that is robust enough for frequent use, easily adjustable to different therapy plans, and portable for multi-location use is essential to maximize therapy effectiveness and operational efficiency.
Pediatric Research Institutes
Research institutes focused on pediatric development utilize sensory training equipment to conduct clinical trials and validate new therapeutic interventions. High-precision tools that can integrate with data collection systems are necessary to monitor progress and outcomes accurately. Buyers internationally must seek suppliers who offer reliable, technologically advanced equipment with strong after-sales support to ensure seamless research operations and innovation in therapy methodologies.
Home Healthcare Providers
Home healthcare providers benefit from compact sensory kits, weighted blankets, and simple interactive toys that allow children to continue sensory therapy outside clinical settings. These products empower parents and caregivers to participate actively in therapy, improving consistency and results. For international buyers, especially in emerging markets, it is important to source equipment that is user-friendly, portable, and accompanied by comprehensive instructional materials to support effective home use and caregiver training.
Related Video: Proprioception | Sensory Processing & Pediatric Occupational Therapy
Strategic Material Selection Guide for Sensory Training Equipment for Pediatric Occupational Therapy Clinic Kids Hospital
Material Analysis for Sensory Training Equipment in Pediatric Occupational Therapy Clinics
1. Medical-Grade Silicone
Key Properties: Medical-grade silicone is known for its excellent flexibility, hypoallergenic nature, and resistance to temperature extremes (typically -60°C to +230°C). It is highly resistant to moisture, UV light, and many chemicals, making it ideal for repeated cleaning and sterilization.
Pros & Cons: Silicone’s durability and softness make it perfect for tactile sensory toys and flexible components such as weighted blankets or sensory pillows. It is non-toxic and safe for children, reducing allergy risks. However, manufacturing silicone products can be costlier due to specialized molding processes and material costs. Its elasticity may limit its use in rigid structural components.
Impact on Application: Silicone’s resistance to heat and chemicals allows for easy sanitation, essential in clinical environments. It is suitable for items that require frequent cleaning or contact with skin, such as chewable toys or sensory mats.
International B2B Considerations: Buyers in Africa, South America, the Middle East, and Europe should ensure compliance with international standards such as ASTM F963 (toy safety), ISO 10993 (biocompatibility), and EU REACH regulations for chemical safety. Medical-grade silicone is widely accepted globally but may require certification documentation for import/export. Its higher cost may affect procurement budgets in emerging markets, but its durability justifies the investment.
2. High-Density Polyethylene (HDPE)
Key Properties: HDPE is a thermoplastic polymer known for its high impact resistance, chemical inertness, and moisture resistance. It operates well across a wide temperature range (-100°C to +120°C) and is resistant to most solvents.
Pros & Cons: HDPE is cost-effective, lightweight, and easy to mold, making it suitable for sensory boards, obstacle course components, and durable toys. It is less flexible than silicone but offers excellent structural integrity. However, HDPE can degrade under prolonged UV exposure unless treated, which may limit outdoor use.
Impact on Application: Its robustness and ease of cleaning make HDPE ideal for equipment that undergoes rough handling and frequent disinfection. It is commonly used for rigid sensory furniture or interactive panels.
International B2B Considerations: HDPE products should meet ASTM D4976 or EN 15344 standards for polyethylene materials. In regions with intense sun exposure such as the Middle East and parts of Africa, UV-stabilized HDPE is recommended. Buyers should verify local import regulations and certifications, especially regarding food-grade or medical-grade classifications if applicable.
3. Polycarbonate (PC)
Key Properties: Polycarbonate is a transparent thermoplastic with high impact resistance, excellent dimensional stability, and good thermal resistance (up to 135°C). It offers superior clarity and toughness compared to other plastics.
Pros & Cons: PC is ideal for sensory light tubes, bubble walls, and interactive equipment requiring transparency and durability. It withstands repeated cleaning and moderate chemical exposure but is prone to scratching and can yellow over time if exposed to UV light without additives.
Impact on Application: Its optical clarity enhances visual sensory stimulation devices, making it a preferred choice for light-based sensory equipment. The material’s strength ensures safety in active play environments.
International B2B Considerations: Compliance with ISO 10993 for biocompatibility and EN 71 for toy safety is critical. PC’s higher price point and manufacturing complexity may influence procurement decisions in budget-sensitive markets. Importers in Europe and Australia often require compliance with RoHS and REACH directives for polycarbonate products.
4. Natural Rubber Latex (with caution)
Key Properties: Natural rubber latex is elastic, soft, and provides excellent tactile feedback. It is biodegradable and offers good resistance to abrasion and tearing but is sensitive to heat and UV light.
Pros & Cons: Latex is cost-effective and provides a natural sensory experience, useful for tactile toys and therapy putty coverings. However, latex allergies are a significant concern, especially in clinical settings. Its durability is lower compared to synthetic alternatives, and it requires careful storage to avoid degradation.
Impact on Application: Latex is best suited for low-risk, short-term use items where tactile sensation is prioritized. It is less suitable for equipment requiring frequent sterilization or long-term durability.
International B2B Considerations: Buyers must be aware of allergy risks and regulatory restrictions on latex use in healthcare products, especially in Europe and Australia. Certification for allergen labeling and compliance with ASTM D1076 or equivalent standards is essential. Due to these concerns, many buyers prefer synthetic alternatives in pediatric therapy environments.
Summary Table of Materials for Sensory Training Equipment
Material | Typical Use Case for Sensory Training Equipment for Pediatric Occupational Therapy Clinic Kids Hospital | Key Advantage | Key Disadvantage/Limitation | Relative Cost (Low/Med/High) |
---|---|---|---|---|
Medical-Grade Silicone | Flexible sensory toys, weighted blankets, chewable items | Hypoallergenic, heat and chemical resistant | Higher manufacturing cost, limited rigidity | High |
High-Density Polyethylene (HDPE) | Rigid sensory boards, obstacle course components, durable toys | Cost-effective, impact resistant, easy to clean | UV degradation without stabilization | Low |
Polycarbonate (PC) | Transparent sensory light tubes, bubble walls, interactive equipment | High impact resistance, optical clarity | Prone to scratching, higher cost, UV yellowing | High |
Natural Rubber Latex | Tactile toys, therapy putty coverings | Excellent tactile feedback, biodegradable | Allergy risk, lower durability, heat sensitive | Low |
This guide provides international B2B buyers with a strategic overview to select materials that best align with their clinical needs, budget constraints, and regional compliance requirements for pediatric sensory training equipment.
In-depth Look: Manufacturing Processes and Quality Assurance for Sensory Training Equipment for Pediatric Occupational Therapy Clinic Kids Hospital
Manufacturing Processes for Sensory Training Equipment
The production of sensory training equipment for pediatric occupational therapy clinics involves meticulous processes to ensure safety, durability, and therapeutic efficacy. This equipment often includes a variety of items such as weighted blankets, tactile toys, sensory mats, and interactive light panels, each requiring specialized manufacturing approaches. Understanding the key manufacturing stages helps international B2B buyers assess supplier capabilities and product quality.
1. Material Preparation
Raw materials selection is critical. High-grade, non-toxic, hypoallergenic materials are preferred to meet pediatric safety requirements. Common materials include medical-grade plastics, soft textiles, silicone, and durable metals. Suppliers typically source these materials from certified vendors who provide compliance documentation on chemical safety and environmental standards. Material preparation includes cutting, molding, or treating components to enhance durability and sensory functionality (e.g., textures or resistance levels).
2. Forming and Fabrication
This stage transforms raw materials into component parts through techniques such as injection molding for plastic parts, fabric cutting and sewing for soft goods, and metal stamping or welding for structural elements. Precision forming is essential to ensure consistent shapes and tactile features that meet therapeutic needs. Advanced methods like 3D printing may be used for custom or small-batch sensory tools, enabling rapid prototyping and design customization.
3. Assembly
Components are assembled manually or via automated lines depending on product complexity and volume. For sensory equipment, assembly often involves combining electronic elements (LED lights, sensors) with physical parts (frames, covers). Strict hygiene and anti-static protocols are maintained to protect sensitive electronic parts and ensure clean, safe products. Ergonomic design considerations are integrated here to ensure equipment is child-friendly and easy for therapists to use.
4. Finishing and Packaging
Finishing includes surface treatments such as polishing, painting with child-safe coatings, and quality labeling. Packaging is designed not only to protect the equipment during shipping but also to convey compliance certifications and user instructions. Eco-friendly and tamper-evident packaging solutions are increasingly preferred, aligning with global sustainability trends and customer expectations.
Quality Assurance and Control (QA/QC)
For B2B buyers, especially in regions like Africa, South America, the Middle East, and Europe, robust quality assurance and control systems are non-negotiable. These systems safeguard against defects and ensure that sensory training equipment meets international safety and performance standards critical for pediatric use.

Illustrative Image (Source: Google Search)
Relevant International and Industry Standards
– ISO 9001: A fundamental quality management system standard that ensures suppliers have documented, consistent processes for product quality.
– CE Marking: Mandatory for products sold within the European Economic Area, indicating conformity with health, safety, and environmental protection standards.
– EN Standards: Specific European standards related to toys and medical devices (e.g., EN 71 for toy safety, EN ISO 13485 for medical devices).
– FDA Compliance (where applicable): For products entering markets like the USA, adherence to FDA medical device regulations may be required.
– RoHS and REACH: Environmental compliance concerning hazardous substances and chemical safety, relevant for electronics in sensory equipment.
Key Quality Control Checkpoints
– Incoming Quality Control (IQC): Verification of raw materials and components before production begins. This includes checking certificates of analysis, material properties, and visual inspections.
– In-Process Quality Control (IPQC): Continuous monitoring during manufacturing to detect defects early. IPQC includes dimensional checks, functional tests (e.g., light intensity for LED panels), and assembly integrity.
– Final Quality Control (FQC): Comprehensive testing of the finished product. This may involve mechanical stress tests, electrical safety tests, sensory feedback validation, and packaging inspection.
Common Testing Methods
– Mechanical Durability Testing: Ensures equipment withstands repeated use and stress without failure. For example, weighted blankets are tested for seam strength and weight distribution consistency.
– Electrical Safety Testing: For interactive sensory devices, tests verify insulation resistance, grounding continuity, and absence of electrical hazards.
– Material Safety Testing: Includes chemical analysis to confirm absence of toxic substances and allergenic potential, critical for pediatric products.
– Functional Performance Testing: Assesses if the equipment delivers the intended sensory input, such as vibration frequency for sensory mats or light spectrum for LED devices.
Verifying Supplier Quality Controls for International B2B Buyers
For buyers operating in diverse regulatory environments, verifying supplier quality controls extends beyond certificates. A multi-faceted approach ensures confidence in product integrity and regulatory compliance.
1. Supplier Audits
Conducting on-site or virtual audits is the most effective way to validate manufacturing processes and QC systems. Audits should cover supplier certifications, process documentation, staff training, and traceability procedures. Buyers can engage third-party audit firms specializing in medical or therapeutic equipment manufacturing to provide unbiased assessments.
2. Reviewing QC Documentation and Test Reports
Request detailed QC records including batch inspection reports, material test certificates, and product sample test results. These documents provide transparency on manufacturing consistency and compliance with required standards.
3. Third-Party Inspections and Certifications
Engaging independent inspection agencies to perform random batch testing or pre-shipment inspections adds a layer of assurance. Certification from recognized bodies (e.g., SGS, TÜV, Intertek) confirms adherence to international safety and quality norms.
4. Sample Testing and Pilot Orders
Before large-scale procurement, buyers should request product samples for in-house testing or clinical evaluation. This step is vital to assess ergonomic suitability, durability, and sensory functionality in the intended therapeutic environment.
Quality Control and Certification Nuances for Buyers from Africa, South America, Middle East, and Europe
Regulatory Landscape Considerations
– Africa: Regulatory frameworks vary widely; some countries rely on international standards like ISO and CE, while others require local certification. Buyers should verify local import regulations and work with suppliers experienced in navigating these markets.
– South America: Countries such as Brazil and Argentina have stringent medical device regulations. Suppliers must often provide documentation in Spanish or Portuguese and comply with ANVISA or equivalent agencies’ standards.
– Middle East: Compliance with GCC Conformity Mark (G Mark) is critical for Gulf countries. Buyers should ensure suppliers meet both international standards and regional requirements.
– Europe: The EU MDR (Medical Device Regulation) governs pediatric therapeutic equipment. CE marking and compliance with EN standards are mandatory. Buyers must confirm suppliers’ readiness for ongoing regulatory audits and post-market surveillance obligations.
Logistical and Documentation Challenges
International buyers should prioritize suppliers offering full transparency in product traceability, certification validity, and after-sales support documentation. Multi-language manuals and compliance documents tailored to regional standards ease customs clearance and end-user adoption.
Sustainability and Ethical Manufacturing
Increasingly, buyers from these regions seek suppliers committed to sustainable practices and ethical labor standards. Certifications such as ISO 14001 (environmental management) and SA8000 (social accountability) can differentiate reputable manufacturers.
Summary Recommendations for B2B Buyers
- Evaluate supplier manufacturing capabilities across all stages: material sourcing, forming, assembly, and finishing.
- Verify certifications and compliance with international and regional standards relevant to pediatric sensory equipment.
- Insist on comprehensive QC documentation and conduct audits or third-party inspections to verify quality claims.
- Request product samples for functional testing aligned with your clinic’s therapeutic goals.
- Understand local regulatory nuances in your target market to ensure smooth import and legal compliance.
- Consider sustainability and ethical manufacturing as part of supplier evaluation to align with global procurement best practices.
By integrating these insights into supplier selection and procurement strategies, international B2B buyers can confidently source high-quality sensory training equipment that meets stringent safety, performance, and regulatory requirements essential for pediatric occupational therapy clinics and children’s hospitals worldwide.
Related Video: SMART Quality Control for Manufacturing
Comprehensive Cost and Pricing Analysis for Sensory Training Equipment for Pediatric Occupational Therapy Clinic Kids Hospital Sourcing
Understanding the intricate cost structure and pricing dynamics for sensory training equipment in pediatric occupational therapy clinics and kids hospitals is crucial for international B2B buyers aiming to optimize procurement decisions. This analysis dissects the key cost components, pricing influencers, and strategic buyer tips tailored especially for markets in Africa, South America, the Middle East, and Europe.
Key Cost Components in Sensory Training Equipment
-
Materials
The raw materials used—such as durable plastics, non-toxic silicone, soft textiles, and specialized lighting components—form the bulk of direct costs. High-quality, hypoallergenic, and certified-safe materials often command premium pricing but ensure safety and longevity critical for pediatric use. -
Labor
Skilled labor for assembly, quality checks, and packaging is a significant cost factor, especially for complex sensory devices incorporating electronics or intricate mechanical parts. Labor costs vary widely by manufacturing region, influencing the final price. -
Manufacturing Overhead
Overheads include utilities, factory maintenance, and indirect labor. Factories with advanced automation may reduce overhead per unit, while artisanal or highly customized equipment often incurs higher overhead costs. -
Tooling and Equipment
Initial tooling, molds, and setup costs for sensory equipment production can be substantial, especially for customized or innovative designs. These costs are amortized over production volumes, impacting the per-unit price. -
Quality Control (QC)
Rigorous QC processes are essential due to the sensitive nature of pediatric therapy equipment. Costs include testing materials for safety standards (e.g., EN71, ASTM), functional testing, and certifications, which add to the overall expense but are non-negotiable for clinical use. -
Logistics and Shipping
International shipping costs, customs duties, insurance, and warehousing can significantly add to the landed cost. Sensory equipment often requires careful packaging to prevent damage, increasing logistics expenses. -
Supplier Margin
Suppliers typically build in margins to cover business risks and profits. Margins may fluctuate based on market demand, exclusivity of the product, and supplier reputation.
Critical Pricing Influencers for International Buyers
-
Order Volume and Minimum Order Quantity (MOQ)
Larger orders usually reduce unit costs through economies of scale. Buyers should negotiate MOQ terms that align with their clinic’s capacity without incurring unnecessary inventory holding costs. -
Product Specifications and Customization
Tailored equipment with specific sensory features or branding commands higher prices. Standardized products offer cost savings but may not meet all therapeutic needs. -
Material Quality and Certifications
Certified materials (e.g., hypoallergenic, flame retardant) and compliance with international pediatric safety standards elevate costs but reduce long-term liability and enhance patient trust. -
Supplier Location and Capabilities
Suppliers in regions with lower labor costs (e.g., Southeast Asia) may offer cheaper pricing but consider trade-offs in lead times and quality control. European or Australian suppliers may provide higher quality assurance at premium prices. -
Incoterms and Delivery Terms
Terms such as FOB, CIF, or DDP affect the buyer’s responsibility and cost exposure. For example, DDP (Delivered Duty Paid) simplifies import logistics but typically costs more upfront.
Strategic Tips for B2B Buyers in Africa, South America, Middle East, and Europe
-
Negotiate Beyond Price:
Engage suppliers on payment terms, volume discounts, warranty periods, and after-sales support to maximize value. -
Evaluate Total Cost of Ownership (TCO):
Factor in maintenance, replacement parts, energy consumption (for electronic sensory devices), and expected lifespan rather than just upfront costs. -
Leverage Group Purchasing:
Clinics and hospitals can collaborate regionally to consolidate orders, reducing MOQs and securing better pricing. -
Understand Import Regulations:
Compliance with local import duties, taxes, and certification requirements is essential to avoid unexpected costs or shipment delays. -
Request Samples and Pilot Runs:
Prior to large orders, testing samples ensures product suitability and quality, reducing the risk of costly returns or dissatisfaction. -
Consider Currency Fluctuations:
Lock in favorable exchange rates where possible, especially when sourcing from volatile currency regions.
Indicative Pricing Disclaimer
Prices for sensory training equipment vary widely based on product type, customization, and sourcing region. The figures discussed here serve as general guidance; buyers should request detailed quotes from multiple suppliers and perform due diligence tailored to their specific clinical needs and regional market conditions.
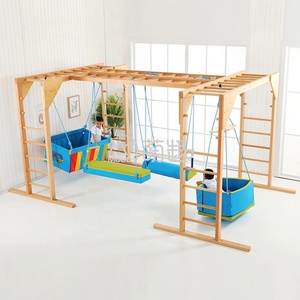
Illustrative Image (Source: Google Search)
By carefully analyzing these cost elements and pricing influencers, international B2B buyers can make informed procurement decisions that balance quality, safety, and cost-efficiency—ultimately enhancing therapeutic outcomes for pediatric patients.
Spotlight on Potential Sensory Training Equipment for Pediatric Occupational Therapy Clinic Kids Hospital Manufacturers and Suppliers
This section looks at several manufacturers active in the ‘Sensory Training Equipment for Pediatric Occupational Therapy Clinic Kids Hospital’ market. This is a representative sample for illustrative purposes; B2B buyers must conduct extensive due diligence before any transaction. Information is synthesized from public sources and general industry knowledge.
Sensory Room Equipment (OT Recommendations)
Detailed public information about this company is limited. It is recommended to visit their website directly for inquiries.
- 🌐 Domain: theottoolbox.com
- 📅 Creation Year: 2017
- ⏳ Registered For: ~8.5 years
Summit Sensory Gym
Summit Sensory Gym specializes in innovative sensory training equipment designed for pediatric occupational therapy clinics, schools, and hospitals. Their product range includes versatile therapy gyms, mobile swing frames, universal exercise units, and sensory mats, supporting multi-disciplinary therapy settings. They cater to educational institutions, outpatient practices, and hospital systems worldwide, enhancing therapeutic outcomes.
- 🌐 Domain: summitsensory.com
- 📅 Creation Year: 2020
- ⏳ Registered For: ~5.0 years
10 Products Every Pediatric Occupational Therapy Clinic Needs
Performance Health specializes in providing a comprehensive range of sensory training and pediatric occupational therapy equipment designed to enhance developmental outcomes in clinical settings. Their product portfolio supports sensory integration, motor skills, and functional independence, catering to pediatric therapy clinics and kids’ hospitals globally, including markets across Africa, South America, the Middle East, and Europe.
- 🌐 Domain: performancehealth.com
- 📅 Creation Year: 2002
- ⏳ Registered For: ~23.2 years
Essential Technical Properties and Trade Terminology for Sensory Training Equipment for Pediatric Occupational Therapy Clinic Kids Hospital
Critical Technical Properties of Sensory Training Equipment
When sourcing sensory training equipment for pediatric occupational therapy clinics and kids hospitals, international B2B buyers must prioritize specific technical properties to ensure safety, durability, and therapeutic effectiveness.
-
Material Grade and Safety Standards
Equipment should be made from non-toxic, hypoallergenic, and durable materials such as medical-grade silicone, BPA-free plastics, or reinforced fabrics. Compliance with international safety certifications (e.g., CE marking for Europe, ASTM standards for the US) is essential to guarantee child safety and regulatory approval across regions like Africa, South America, and the Middle East. -
Weight and Load Tolerance
Sensory equipment like swings, trampolines, or weighted vests must specify maximum weight limits and tolerance thresholds. This ensures safe use by children of varying ages and sizes and prevents structural failure during therapy sessions, which is critical for liability management and long-term investment protection. -
Adjustability and Modularity
Equipment with adjustable resistance, height, or sensory input levels supports individualized therapy plans. Modularity allows clinics to customize or upgrade components (e.g., interchangeable tactile panels or light modules), maximizing value and adaptability to diverse pediatric needs. -
Durability and Maintenance Requirements
Since pediatric clinics experience high equipment usage, durability against wear and tear is vital. Materials should resist staining, impact, and moisture. Additionally, equipment designed for easy cleaning and maintenance reduces downtime and operational costs, a key consideration for budget-conscious buyers in emerging markets. -
Sensory Stimulation Specifications
For light-based or interactive equipment, technical details like LED lifespan, brightness levels (measured in lumens), and sound frequency ranges are important. These parameters impact therapeutic outcomes and energy efficiency, influencing both clinical effectiveness and utility expenses. -
Size and Space Efficiency
Compact or foldable designs are advantageous for clinics with limited space, common in many hospitals worldwide. Accurate dimensions and storage requirements must be communicated clearly to facilitate logistical planning and installation.
Key Trade Terminology for International B2B Buyers
Understanding industry jargon can streamline communication with manufacturers and suppliers, ensuring smoother procurement processes.
-
OEM (Original Equipment Manufacturer)
Refers to companies that design and produce equipment which other brands re-label and sell. Buyers may opt for OEM products to customize branding or negotiate cost advantages. Knowing if a supplier is OEM-certified helps verify product authenticity and quality. -
MOQ (Minimum Order Quantity)
The smallest quantity a supplier is willing to sell in one order. MOQs vary widely and can affect upfront investment and inventory management. Buyers from smaller clinics or emerging markets should negotiate MOQs that align with their capacity and demand forecasts. -
RFQ (Request for Quotation)
A formal document sent to suppliers to obtain pricing, lead times, and terms for specified products. Precise RFQs including detailed technical specifications help secure accurate and competitive offers, minimizing back-and-forth and delays. -
Incoterms (International Commercial Terms)
Standardized trade terms defining responsibilities for shipping, insurance, and customs between buyers and sellers. Common terms include FOB (Free On Board), CIF (Cost, Insurance, and Freight), and DDP (Delivered Duty Paid). Understanding Incoterms is crucial for cost calculation and risk management across international borders. -
Lead Time
The time from order placement to delivery. Critical for planning therapy program rollouts or replenishing consumables. Buyers should confirm lead times upfront to avoid disruptions in clinical operations. -
Certification and Compliance
This term covers documentation proving that equipment meets safety, environmental, or regional regulatory requirements. Certifications like CE, ISO 13485 (medical devices), or RoHS (restriction of hazardous substances) assure buyers of product legitimacy and facilitate import clearance.
By mastering these technical properties and trade terms, international B2B buyers can make informed purchasing decisions that optimize therapeutic outcomes, ensure compliance, and enhance operational efficiency in pediatric occupational therapy settings.
Navigating Market Dynamics, Sourcing Trends, and Sustainability in the Sensory Training Equipment for Pediatric Occupational Therapy Clinic Kids Hospital Sector
Market Overview & Key Trends
The global market for sensory training equipment in pediatric occupational therapy clinics and kids’ hospitals is experiencing robust growth, driven by increasing awareness of neurodevelopmental disorders and a growing emphasis on early intervention. International B2B buyers from Africa, South America, the Middle East, and Europe are tapping into this expanding sector to meet rising demand for innovative therapeutic tools tailored to children with sensory processing challenges.
Key market drivers include government initiatives to improve pediatric healthcare infrastructure, rising investments in specialized therapy centers, and increasing prevalence of conditions such as autism spectrum disorders and ADHD. Buyers in emerging regions like South Africa and parts of Latin America are prioritizing equipment that is both multifunctional and adaptable to diverse clinical settings, while European and Middle Eastern buyers often seek cutting-edge, technology-integrated solutions that enhance therapeutic engagement and data tracking.
Current sourcing trends reveal a shift toward modular, customizable sensory equipment that supports a wide range of therapies—from vestibular and proprioceptive to tactile and visual stimulation. Interactive sensory walls, fiber optic lighting systems, weighted blankets, and digital projection tools are gaining traction for their proven efficacy and child-friendly designs. Additionally, there is a growing preference for suppliers offering end-to-end solutions, including installation, training, and after-sales support, which is critical for markets with developing occupational therapy sectors.
Technological advancements such as IoT-enabled sensory devices and virtual reality integration are emerging, albeit at a slower pace in regions with limited digital infrastructure. B2B buyers are increasingly leveraging virtual demos and digital catalogs to streamline procurement and ensure compliance with local regulatory standards. Partnerships with local distributors and customization capabilities are becoming essential to navigate import restrictions and meet region-specific clinical requirements.
Sustainability & Ethical Sourcing in B2B
Sustainability and ethical sourcing have become pivotal considerations for international buyers of sensory training equipment, reflecting broader global commitments to environmental stewardship and social responsibility. Pediatric occupational therapy clinics and hospitals are prioritizing products manufactured using non-toxic, hypoallergenic, and recyclable materials that ensure safety for vulnerable pediatric populations and minimize ecological footprints.
Environmental impact concerns drive demand for equipment made from sustainable raw materials such as organic cotton, natural rubber, and biodegradable plastics. Buyers increasingly expect suppliers to provide certifications like FSC (Forest Stewardship Council) for wooden components, OEKO-TEX for textiles, and RoHS compliance for electronic devices, which guarantee adherence to environmental and health safety standards.
Ethical sourcing extends beyond materials to include fair labor practices and transparent supply chains. B2B buyers, especially from Europe and Australia, are scrutinizing suppliers for compliance with international labor laws and corporate social responsibility commitments. This scrutiny helps mitigate risks related to child labor, unsafe working conditions, and supply chain disruptions.
Moreover, green manufacturing processes—such as energy-efficient production, waste reduction, and water conservation—are becoming decisive factors in vendor selection. Buyers are also encouraging suppliers to adopt circular economy principles, such as take-back programs and refurbishing initiatives, to extend product life cycles. Sustainability in sensory equipment not only aligns with institutional values but also enhances brand reputation and compliance with increasingly stringent public procurement policies.
Evolution of Sensory Training Equipment in Pediatric Occupational Therapy
Sensory training equipment has evolved significantly from rudimentary tools to sophisticated, multi-sensory systems designed to address complex developmental needs. Historically, pediatric occupational therapy relied on basic tactile and proprioceptive aids such as textured balls and swings. Over time, advancements in neuroscience and therapy methodologies spurred the development of specialized equipment integrating visual, auditory, and vestibular stimuli.
The introduction of sensory rooms equipped with bubble tubes, fiber optic lights, and interactive walls marked a turning point, enabling immersive therapeutic environments that facilitate sensory integration more effectively. Digital innovations, including interactive floor projectors and IoT-connected devices, now offer real-time feedback and customizable therapy sessions, enhancing outcomes and engagement.
For international B2B buyers, understanding this evolution underscores the importance of sourcing equipment that not only meets current therapeutic standards but is also adaptable to future technological advancements and evolving clinical protocols. This historical context supports informed procurement decisions that balance innovation, safety, and long-term value.
Related Video: Tactile | Sensory Processing & Pediatric Occupational Therapy
Frequently Asked Questions (FAQs) for B2B Buyers of Sensory Training Equipment for Pediatric Occupational Therapy Clinic Kids Hospital
-
How can I effectively vet suppliers of sensory training equipment for pediatric occupational therapy clinics internationally?
To vet suppliers, start by verifying their certifications such as ISO 9001 for quality management and compliance with international safety standards like CE or ASTM. Request detailed product catalogs, client references, and evidence of previous exports, especially to healthcare or pediatric therapy sectors. Conduct virtual or in-person factory audits if feasible. Check responsiveness and transparency regarding material sourcing and manufacturing processes. Collaborating with suppliers who have experience in your region (Africa, South America, Middle East, Europe) helps ensure they understand local regulatory and logistical requirements. -
Is it possible to customize sensory training equipment to meet specific therapeutic needs or regional preferences?
Yes, many reputable manufacturers offer customization options including size, materials, colors, and sensory features to align with therapy goals or cultural preferences. Customization can extend to branding, packaging, and compliance with local safety standards. When negotiating customization, clarify minimum order quantities (MOQs), lead times, and cost implications upfront. Providing detailed specifications or involving your occupational therapists early in the process ensures the equipment supports targeted pediatric interventions effectively. -
What are typical minimum order quantities (MOQs) and lead times for international orders of sensory equipment?
MOQs vary widely depending on product complexity and customization level, ranging from small batches of 10–50 units for simpler items (e.g., fidget toys) to hundreds for larger or custom sensory gym equipment. Lead times typically span 4–12 weeks, influenced by production schedules, customization, and shipping logistics. Planning orders well in advance and maintaining clear communication with suppliers helps manage expectations. Some suppliers may offer sample orders or phased deliveries to mitigate upfront investment risk. -
Which payment terms are standard for international B2B transactions in this sector, and how can I mitigate payment risks?
Common payment terms include 30% upfront deposit with balance paid upon shipment or after inspection. Letters of credit (LC) and escrow services are often used to protect both parties. To reduce risk, verify supplier credentials, use secure payment platforms, and consider trade credit insurance. Establishing long-term relationships can facilitate more flexible terms. Always include detailed contracts specifying delivery milestones, quality requirements, and dispute resolution processes to safeguard your investment. -
What quality assurance (QA) and certification requirements should I insist on for sensory training equipment?
Insist on compliance with international safety standards like CE marking (Europe), FDA or ASTM standards (US), and ISO 13485 for medical devices. QA processes should include raw material testing, in-process inspections, and final product testing for durability, safety, and hygiene. Request third-party lab test reports or factory audit results. Certifications related to non-toxicity, hypoallergenic materials, and electrical safety (for light or interactive equipment) are critical. Ensuring traceability and warranty coverage further protects your procurement. -
How should I approach logistics and shipping challenges for bulky or sensitive sensory equipment internationally?
Choose suppliers experienced with international freight forwarding and familiar with your destination country’s import regulations, customs clearance, and taxes. For fragile or electronic sensory equipment, confirm appropriate packaging standards and consider insurance for transit damage. Sea freight is economical for large shipments but slower; air freight suits urgent or smaller consignments. Collaborate with logistics providers offering end-to-end tracking and support local warehousing if needed to streamline distribution to clinics or hospitals. -
What strategies can help resolve disputes related to product quality or delivery delays with overseas suppliers?
Establish clear contracts detailing product specifications, delivery schedules, and penalties for non-compliance. Maintain regular communication and document all interactions. If issues arise, promptly request corrective action or replacements supported by photographic evidence or inspection reports. Employ mediation or arbitration clauses specifying neutral jurisdictions and languages to avoid costly litigation. Building a relationship based on trust and transparency can facilitate amicable solutions and prevent escalation. -
Are there specific considerations when sourcing sensory training equipment for pediatric occupational therapy clinics in Africa, South America, the Middle East, and Europe?
Yes, regional factors like electrical standards, climate durability, cultural preferences, and language impact product suitability and supplier selection. For example, equipment with adjustable voltage or climate-resistant materials is important in Africa and the Middle East. Understanding local regulatory frameworks and import tariffs is essential. Partnering with suppliers who offer multilingual support, regional warehouses, or local agents can improve service and reduce lead times. Also, consider after-sales support and training tailored to local therapists’ needs.
Important Disclaimer & Terms of Use
⚠️ Important Disclaimer
The information provided in this guide, including content regarding manufacturers, technical specifications, and market analysis, is for informational and educational purposes only. It does not constitute professional procurement advice, financial advice, or legal advice.
While we have made every effort to ensure the accuracy and timeliness of the information, we are not responsible for any errors, omissions, or outdated information. Market conditions, company details, and technical standards are subject to change.
B2B buyers must conduct their own independent and thorough due diligence before making any purchasing decisions. This includes contacting suppliers directly, verifying certifications, requesting samples, and seeking professional consultation. The risk of relying on any information in this guide is borne solely by the reader.
Strategic Sourcing Conclusion and Outlook for Sensory Training Equipment for Pediatric Occupational Therapy Clinic Kids Hospital
Strategic sourcing of sensory training equipment for pediatric occupational therapy clinics and kids’ hospitals is pivotal for delivering impactful therapeutic outcomes. Key takeaways for international B2B buyers include prioritizing equipment that is versatile, evidence-based, and customizable to diverse pediatric needs, while ensuring compliance with safety and quality standards relevant to each region. Leveraging suppliers who offer comprehensive product ranges—from sensory lights and interactive toys to weighted garments and adaptive furniture—can streamline procurement and enhance clinical efficacy.
For buyers across Africa, South America, the Middle East, and Europe, embracing strategic partnerships with manufacturers and distributors experienced in pediatric sensory solutions will help navigate logistical complexities and import regulations effectively. Additionally, investing in durable, easy-to-maintain equipment supports long-term cost efficiency and sustainability in clinical settings.
Looking ahead, the growing global focus on pediatric occupational therapy and sensory integration underscores a rising demand for innovative, technology-enhanced products. Buyers are encouraged to stay informed about emerging trends such as interactive sensory environments and digital therapy aids. By adopting a proactive sourcing strategy that balances quality, cost, and regional adaptability, international stakeholders can significantly improve therapeutic services and outcomes for children worldwide. Engage with trusted suppliers today to future-proof your clinic’s sensory training capabilities and advance pediatric care excellence.