Article Navigation
- Introduction: Navigating the Global Market for sensory Spinning chair
- Understanding sensory Spinning chair Types and Variations
- Key Industrial Applications of sensory Spinning chair
- Strategic Material Selection Guide for sensory Spinning chair
- In-depth Look: Manufacturing Processes and Quality Assurance for sensory Spinning chair
- Comprehensive Cost and Pricing Analysis for sensory Spinning chair Sourcing
- Spotlight on Potential sensory Spinning chair Manufacturers and Suppliers
- Essential Technical Properties and Trade Terminology for sensory Spinning chair
- Navigating Market Dynamics, Sourcing Trends, and Sustainability in the sensory Spinning chair Sector
- Frequently Asked Questions (FAQs) for B2B Buyers of sensory Spinning chair
- Important Disclaimer & Terms of Use
- Strategic Sourcing Conclusion and Outlook for sensory Spinning chair
Introduction: Navigating the Global Market for sensory Spinning chair
The global demand for sensory spinning chairs is rapidly expanding as businesses and institutions recognize their critical role in enhancing focus, comfort, and sensory regulation for diverse user groups, including neurodivergent individuals. For international B2B buyers—particularly those operating in dynamic markets across Africa, South America, the Middle East, and Europe—sourcing the right sensory spinning chair is a strategic decision that directly impacts product effectiveness, user satisfaction, and market competitiveness.
Sensory spinning chairs are specialized seating solutions designed to provide calming motion and proprioceptive feedback, supporting environments such as educational facilities, therapy centers, and inclusive workplaces. Their ability to improve concentration and reduce sensory overload makes them invaluable assets in neurodiversity-friendly spaces, which are increasingly prioritized worldwide. As such, understanding the nuances of product types, material compositions, manufacturing quality controls, and supplier reliability is essential for buyers aiming to optimize their procurement processes.
This comprehensive guide equips B2B buyers with in-depth insights into the sensory spinning chair market, including detailed evaluations of various chair designs and materials, key manufacturing standards, quality assurance practices, and cost considerations. Additionally, it offers a regional market overview to help buyers from Vietnam to France identify trends and sourcing opportunities that align with their unique market demands. A dedicated FAQ section further clarifies common concerns, ensuring informed decision-making.
By leveraging this resource, international buyers can confidently navigate the complexities of global sourcing, secure competitive pricing, and establish partnerships with reputable manufacturers. Ultimately, this guide empowers businesses to deliver superior sensory seating solutions that meet evolving client needs and support inclusive, productive environments worldwide.
Understanding sensory Spinning chair Types and Variations
Type Name | Key Distinguishing Features | Primary B2B Applications | Brief Pros & Cons for Buyers |
---|---|---|---|
Basic Sensory Spinning Chair | Simple swivel base with smooth 360-degree rotation; minimal cushioning | Educational institutions, therapy centers | + Cost-effective, versatile; – Limited sensory input variety |
Therapeutic Compression Spinning Chair | Incorporates compression features providing a hugging sensation along with spinning | Healthcare facilities, sensory therapy providers | + Enhances sensory regulation; – Higher cost, bulkier design |
Active Movement Spinning Chair | Designed to encourage micro-movements like wobbling or rocking combined with spinning | Special education classrooms, occupational therapy | + Promotes focus and motor skills; – May not suit all physical abilities |
Multi-Sensory Spinning Chair | Integrates spinning with additional sensory stimuli such as tactile surfaces or vibration | Autism support centers, neurodivergent workspaces | + Multifunctional sensory engagement; – Complexity increases price and maintenance |
Adjustable Height & Support Spinning Chair | Features customizable height and ergonomic support alongside spinning function | Corporate offices, inclusive workplaces | + Adaptable for diverse users; – May have higher upfront investment |
Basic Sensory Spinning Chair
These chairs feature a simple swivel base allowing smooth 360-degree rotation, often with minimal cushioning to enable ease of movement. They are widely used in educational and therapeutic settings for children and adults requiring basic sensory input to aid focus and engagement. For B2B buyers, these chairs offer a cost-effective solution with broad applicability but limited sensory stimulation, making them ideal for environments seeking foundational active seating without complex features.
Therapeutic Compression Spinning Chair
Designed to provide both spinning motion and gentle compression, these chairs simulate a comforting hug that aids sensory regulation. They are particularly relevant for healthcare providers and sensory therapy centers working with neurodivergent individuals. Buyers should consider their higher price point and larger footprint but can expect enhanced therapeutic benefits that justify investment in specialized clinical or educational settings.
Active Movement Spinning Chair
This variation encourages additional micro-movements such as wobbling or rocking alongside spinning, supporting motor skills development and sustained attention. They are popular in special education and occupational therapy environments. B2B purchasers should assess the physical ability of users, as these chairs may not suit everyone; however, they provide dynamic sensory input that can improve user engagement and productivity.
Multi-Sensory Spinning Chair
Combining spinning with tactile elements, vibration, or other sensory inputs, these chairs offer comprehensive sensory engagement for neurodivergent workspaces and autism support centers. Their multifunctionality supports diverse sensory needs but comes with increased complexity, cost, and maintenance considerations. Buyers targeting niche markets requiring advanced sensory solutions will find these chairs valuable despite the higher investment.
Adjustable Height & Support Spinning Chair
These chairs incorporate ergonomic features such as adjustable height and lumbar support alongside spinning functionality, making them suitable for inclusive corporate offices and environments prioritizing user comfort and adaptability. While the upfront cost may be higher, the versatility and ergonomic benefits make them a strategic purchase for businesses aiming to accommodate diverse employee needs and enhance workplace well-being.
Related Video: Kids 360 degree sensory spinning swivel chair Amazon review
Key Industrial Applications of sensory Spinning chair
Industry/Sector | Specific Application of sensory Spinning chair | Value/Benefit for the Business | Key Sourcing Considerations for this Application |
---|---|---|---|
Education & Special Needs | Classroom sensory seating for neurodivergent students | Enhances focus, reduces disruptive behavior, improves learning outcomes | Durability, ergonomic design, safety certifications, ease of maintenance, customization options for different sensory needs |
Healthcare & Therapy | Occupational therapy centers for sensory integration therapy | Supports sensory regulation, improves patient engagement and therapy effectiveness | Compliance with medical standards, hygienic materials, adjustable features for diverse patient needs, supplier reliability |
Corporate & Office Spaces | Employee wellness and active seating solutions | Boosts concentration, reduces stress, promotes physical activity during work | Comfort, adjustability, modern aesthetics, durability for heavy use, warranty and after-sales service |
Childcare & Early Learning | Sensory play areas and calming zones | Provides calming stimulation, supports developmental needs, reduces anxiety | Child-safe materials, lightweight design, ease of cleaning, adaptability to different environments |
Public & Community Centers | Inclusive spaces for neurodiverse individuals | Facilitates social inclusion, supports sensory self-regulation, enhances user experience | Robust construction, portability, multi-user capacity, cultural adaptability, competitive pricing |
Education & Special Needs
In educational settings, sensory spinning chairs are increasingly used to support students with autism, ADHD, and other sensory processing disorders. These chairs provide controlled movement and sensory input, helping students to self-regulate and maintain attention during lessons. For international buyers in regions like Africa, South America, and Europe, sourcing chairs with customizable sensory features and durable build quality is critical to accommodate diverse classroom environments and climate conditions. Ergonomic design and compliance with safety standards are essential to ensure long-term usability and student safety.
Healthcare & Therapy
Occupational therapy centers leverage sensory spinning chairs as therapeutic tools to aid sensory integration and motor skills development. These chairs help patients experience calming vestibular stimulation, improving engagement and outcomes in therapy sessions. Buyers from the Middle East and Europe should prioritize sourcing chairs that meet stringent medical safety regulations, incorporate hygienic and easy-to-clean materials, and offer adjustable features to cater to a wide range of patient abilities. Reliable supplier partnerships are vital for consistent product quality and support.
Corporate & Office Spaces
Modern offices adopt sensory spinning chairs as part of active seating initiatives to enhance employee wellness and productivity. These chairs encourage subtle movement, reducing physical discomfort and mental fatigue during long working hours. International businesses, especially in Vietnam and France, must consider ergonomic certifications, aesthetic compatibility with office interiors, and durability under daily use when selecting these chairs. Warranty coverage and after-sales services are key factors for sustained investment value.
Childcare & Early Learning
Sensory spinning chairs play a significant role in childcare centers by creating calming zones and sensory play areas. They provide children with soothing motion that helps manage anxiety and supports developmental milestones. Buyers targeting this sector should focus on chairs made from child-safe, non-toxic materials that are lightweight and easy to clean. Adaptability to various childcare environments and compliance with local safety regulations are important for buyers in emerging markets across Africa and South America.
Public & Community Centers
Community spaces aiming for inclusivity use sensory spinning chairs to create environments welcoming to neurodiverse populations. These chairs enable users to self-regulate sensory input, promoting social participation and comfort. For international buyers, factors such as robust construction for frequent use, portability for flexible space arrangements, and cultural adaptability in design and color are crucial. Competitive pricing and multi-user capacity enhance the appeal for public sector procurement in diverse global regions.
Related Video: Uses and Gratifications Theory – UGT
Strategic Material Selection Guide for sensory Spinning chair
When selecting materials for sensory spinning chairs, international B2B buyers must carefully evaluate the properties that influence durability, comfort, safety, and compliance with regional standards. Below is an analysis of four common materials used in sensory spinning chairs, focusing on their performance, manufacturing implications, and suitability for diverse markets such as Africa, South America, the Middle East, and Europe.
1. High-Density Polyethylene (HDPE)
Key Properties:
HDPE is a thermoplastic polymer known for its excellent impact resistance, chemical inertness, and ability to withstand a wide temperature range (-50°C to 80°C). It offers good moisture resistance and is non-toxic, making it safe for sensory applications.
Pros & Cons:
HDPE is lightweight and cost-effective, simplifying shipping and handling logistics. It is also easy to mold into ergonomic shapes, supporting complex chair designs. However, HDPE can be prone to surface scratching and UV degradation if not properly stabilized, which may reduce longevity in outdoor or high-exposure environments.
Impact on Application:
Its resistance to moisture and chemicals makes HDPE suitable for environments with variable humidity or cleaning requirements, common in healthcare or educational settings. However, it may not provide the premium tactile feel some users expect in high-end sensory chairs.
International Considerations:
HDPE complies with global standards such as ASTM D3350 and EN ISO 1872-2, facilitating import/export across regions. Buyers in Africa and South America benefit from its affordability and ease of maintenance, while European and Middle Eastern markets appreciate its compliance with stringent safety and environmental regulations, including REACH and RoHS.
2. Steel (Powder-Coated or Stainless)
Key Properties:
Steel offers superior structural strength, excellent load-bearing capacity, and high durability. Powder-coated steel provides corrosion resistance, while stainless steel variants offer enhanced resistance to rust and chemical exposure.
Pros & Cons:
Steel frames ensure long-lasting stability and safety, especially important for chairs designed for children or therapeutic use. However, steel is heavier, increasing transportation costs and complicating assembly. Manufacturing involves higher energy consumption and complexity, impacting lead times and cost.
Impact on Application:
Steel is ideal for commercial-grade sensory spinning chairs used in schools, clinics, and therapy centers where robustness is critical. Its rigidity supports dynamic movements without compromising safety.
International Considerations:
Steel materials must meet standards like ASTM A36, EN 10025, or JIS G3101, which are widely recognized internationally. Middle Eastern and European buyers often require certification for powder coatings to ensure hypoallergenic and non-toxic finishes. Corrosion resistance is particularly crucial in humid or coastal African and South American regions.
3. Fabric Upholstery (with High-Resilience Foam)
Key Properties:
Fabric upholstery combined with high-resilience foam offers comfort, breathability, and sensory appeal. Fabrics vary widely, from natural fibers like cotton to synthetic blends with stain-resistant treatments.
Pros & Cons:
This material combination enhances user comfort and can be customized for sensory stimulation through texture and color. However, fabric can be less durable, prone to staining, and may require more frequent cleaning or replacement. Foam density affects longevity and support; low-quality foam can degrade quickly.
Impact on Application:
Fabric-covered sensory chairs are preferred in therapeutic and educational settings where tactile feedback and comfort are prioritized. They are less suitable for outdoor or high-moisture environments unless treated with water-resistant coatings.
International Considerations:
Buyers in Europe and the Middle East often demand compliance with fire safety standards such as BS 5852 or EN 1021. In Africa and South America, considerations include fabric availability, ease of cleaning, and resistance to local environmental factors like dust and humidity. Sustainable and OEKO-TEX certified fabrics are increasingly valued in all regions.
4. Polyurethane (PU) Coated Components
Key Properties:
PU coatings provide a durable, flexible, and abrasion-resistant surface that can mimic leather or other textures. It offers moderate water resistance and can be formulated to meet various hardness and elasticity requirements.
Pros & Cons:
PU-coated materials are easier to clean and maintain than fabric, with better resistance to spills and wear. They offer a premium aesthetic at a moderate cost. However, PU can degrade under prolonged UV exposure and may emit volatile organic compounds (VOCs) if not properly formulated.
Impact on Application:
PU coatings are suitable for sensory chairs requiring a balance between durability and comfort, especially in commercial environments. They are often used in office or classroom settings where frequent cleaning is necessary.
International Considerations:
Compliance with VOC emission standards (e.g., European REACH, California CARB) is critical for buyers in Europe and the Middle East. In tropical African and South American climates, UV resistance and heat tolerance are key factors. PU-coated chairs also appeal to markets seeking easy-to-clean surfaces for hygiene-sensitive applications.
Material | Typical Use Case for sensory Spinning chair | Key Advantage | Key Disadvantage/Limitation | Relative Cost (Low/Med/High) |
---|---|---|---|---|
High-Density Polyethylene (HDPE) | Lightweight, moisture-resistant chair shells for educational and therapeutic use | Cost-effective, chemical and moisture resistant | Susceptible to UV degradation and surface scratching | Low |
Steel (Powder-Coated or Stainless) | Structural frames for commercial-grade, durable sensory chairs | High strength and durability, excellent safety | Heavy, higher manufacturing complexity and cost | High |
Fabric Upholstery with High-Resilience Foam | Comfort-focused sensory chairs in therapy and classroom settings | Enhanced tactile comfort and customization | Lower durability, prone to staining and wear | Medium |
Polyurethane (PU) Coated Components | Chairs requiring durable, easy-to-clean surfaces with premium feel | Abrasion-resistant, easy maintenance | Potential VOC emissions, UV sensitivity | Medium |
In-depth Look: Manufacturing Processes and Quality Assurance for sensory Spinning chair
Manufacturing Processes for Sensory Spinning Chairs
Manufacturing sensory spinning chairs involves a combination of precision engineering, ergonomic design, and quality material selection to meet the unique needs of neurodivergent users and active seating markets. Understanding the production workflow helps B2B buyers assess supplier capabilities and product reliability.
1. Material Preparation
The process starts with sourcing high-grade raw materials:
– Metals: Steel or aluminum alloys are commonly used for the chair’s frame and spinning mechanisms due to their strength and durability.
– Foams and Fabrics: High-density memory foams or compression foams provide sensory feedback and comfort, while durable, hypoallergenic fabrics or synthetic leathers are chosen for upholstery.
– Plastic Components: Molded plastic parts, such as base covers or armrests, are often produced using injection molding techniques.
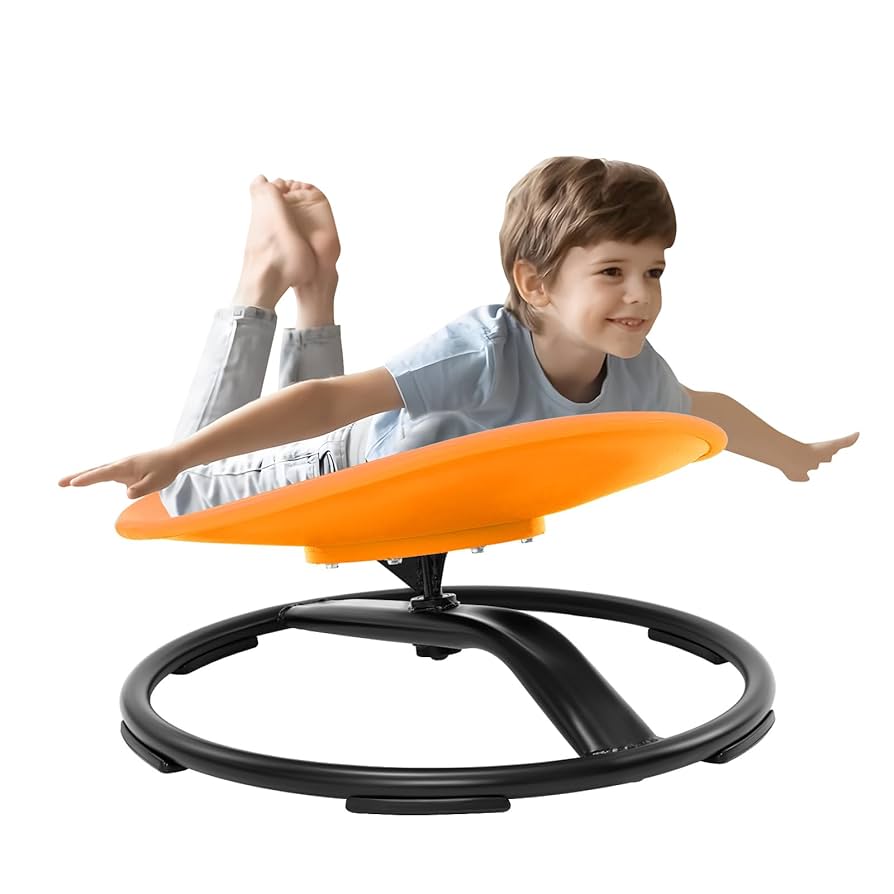
Illustrative Image (Source: Google Search)
Material preparation includes cutting, shaping, and treating these components to ensure they meet specifications for strength, flexibility, and safety.
2. Forming and Component Manufacturing
Key forming techniques include:
– Metal Fabrication: CNC machining, bending, and welding are used to create the chair’s frame and spinning mechanisms. Precision in these steps ensures smooth rotation and structural integrity.
– Foam Molding: Compression or injection molding for foam inserts tailored to provide specific sensory input (e.g., hugging pressure or gentle rocking).
– Textile Processing: Cutting and stitching of upholstery materials with reinforced seams to withstand repeated use and movement.
3. Assembly
Assembly is a critical phase where all components are integrated:
– Frame Assembly: Frames are welded or bolted together and fitted with spinning bearings or swivel mechanisms.
– Cushion and Upholstery Installation: Foam inserts are secured and covered with fabric or leather, often using industrial sewing machines and adhesives.
– Functional Add-ons: Some sensory chairs incorporate features such as weighted covers, vibration modules, or adjustable components to customize sensory input.
Automated and manual assembly lines coexist, depending on order volume and customization needs.
4. Finishing and Quality Treatments
Finishing includes:
– Surface Treatments: Powder coating or electroplating of metal parts to prevent corrosion and enhance aesthetics.
– Inspection of Upholstery: Ensuring fabric consistency, colorfastness, and absence of defects.
– Packaging: Use of protective materials to safeguard the chair during shipping, often including assembly instructions and warranty information.
Quality Assurance and Control (QA/QC) Framework
Robust quality control is essential for sensory spinning chairs, particularly when supplying international markets with diverse regulatory requirements.
International and Industry Standards
- ISO 9001: This global standard for quality management systems ensures consistent production processes, supplier management, and continuous improvement. B2B buyers should verify that manufacturers hold valid ISO 9001 certification.
- CE Marking: For European markets, CE certification indicates compliance with EU safety, health, and environmental protection requirements.
- Other Relevant Certifications: Depending on the application (e.g., therapeutic use), manufacturers may also adhere to standards such as FDA regulations (for medical-grade chairs), ASTM (American Society for Testing and Materials), or specific regional certifications.
QC Checkpoints
- Incoming Quality Control (IQC): Inspection of raw materials and components before production to verify specifications, including metal strength, foam density, and fabric quality.
- In-Process Quality Control (IPQC): Continuous monitoring during assembly stages, such as dimensional accuracy of frames, smoothness of swivel mechanisms, and secure upholstery attachment.
- Final Quality Control (FQC): Comprehensive testing of finished chairs, including load testing, durability under repetitive spinning, sensory feedback validation, and visual inspection for cosmetic defects.
Common Testing Methods
- Load and Stress Testing: Chairs are subjected to static and dynamic loads exceeding typical user weight to confirm structural integrity.
- Spin and Rotation Testing: Ensures smooth, noiseless spinning action with controlled resistance to support active seating needs.
- Material Safety Tests: Verification of non-toxicity, flame retardancy, and hypoallergenic properties of fabrics and foams.
- Ergonomic Assessment: Measurements to confirm that chairs meet ergonomic standards for comfort and support, critical for long-term use by neurodivergent individuals.
How B2B Buyers Can Verify Supplier QC
For buyers, especially in regions such as Africa, South America, the Middle East, and Europe, ensuring supplier QC compliance is crucial for product reliability and regulatory adherence.
1. Request Documentation and Certifications
- Verify ISO 9001 and CE certificates with issuing bodies.
- Request product test reports from accredited labs.
- Ask for compliance documents tailored to your region’s regulations.
2. Conduct Factory Audits
- Arrange on-site audits or remote video inspections focusing on production lines, material storage, and QC stations.
- Evaluate supplier adherence to documented processes and cleanliness standards.
- Review calibration records for testing equipment.
3. Use Third-Party Inspection Services
- Employ independent inspection agencies to perform random sampling and testing.
- Third-party inspectors can provide unbiased reports on product conformity and packaging quality.
- This is especially valuable for first-time orders or new suppliers.
4. Implement Pilot Orders and Sample Testing
- Order prototypes or small batches for in-house testing.
- Evaluate chair durability, sensory functions, and user feedback before scaling orders.
QC and Certification Nuances for International Buyers
Regional Regulatory Variations
- Africa & Middle East: Some countries may require additional certification or local testing to meet import regulations. Buyers should confirm compliance with regional standards such as SASO (Saudi Standards) or ARSO (African Organization for Standardization).
- South America: Certification requirements may include INMETRO (Brazil) or similar bodies. Language and labeling compliance are also important.
- Europe: CE marking is mandatory, with additional emphasis on sustainability and chemical safety (REACH compliance). Buyers in countries like France often require detailed technical dossiers and conformity assessments.
- Vietnam and Asia-Pacific: While not the primary focus, many suppliers here follow ISO and international standards, but buyers should verify local import rules and certification equivalencies.
Language and Documentation
- Ensure all QC reports, certifications, and user manuals are provided in the buyer’s preferred language or English.
- Clear documentation facilitates customs clearance and end-user training.
After-Sales Quality Support
- Confirm supplier commitments to warranty, spare parts availability, and post-sale technical support.
- Good QA practices include traceability of batch numbers and production dates for quality tracking.
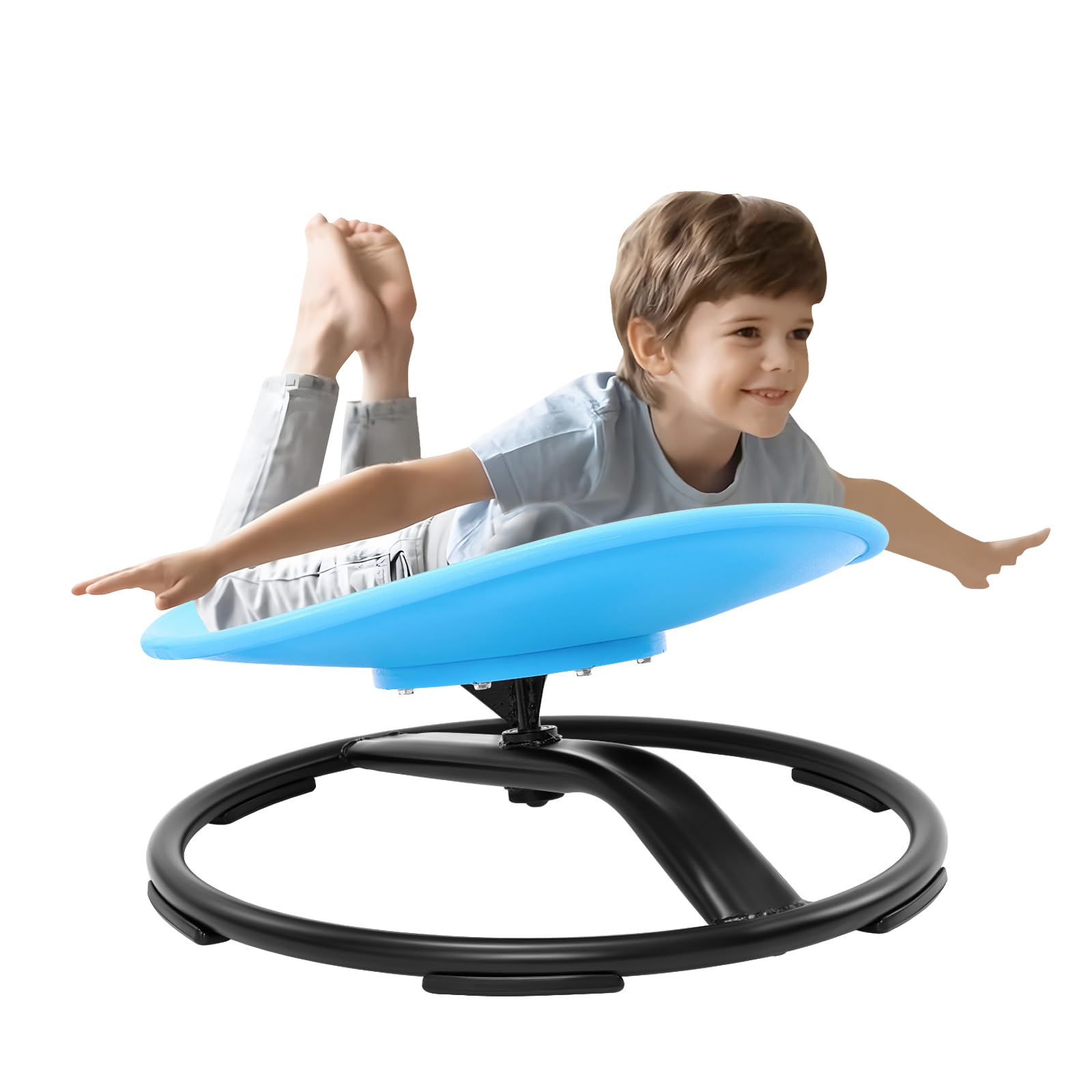
Illustrative Image (Source: Google Search)
Key Takeaways for B2B Buyers
- Insist on ISO 9001 certified manufacturers with proven expertise in ergonomic and sensory product manufacturing.
- Prioritize suppliers who demonstrate rigorous IQC, IPQC, and FQC processes with transparent testing protocols.
- Utilize third-party inspections and factory audits to independently verify supplier claims.
- Understand and comply with regional certification requirements to avoid import delays and ensure market acceptance.
- Evaluate material quality and ergonomic design through sample testing before large orders.
- Foster partnerships with manufacturers that offer comprehensive after-sales support and maintain product traceability.
By carefully assessing manufacturing processes and quality assurance systems, international B2B buyers can confidently source sensory spinning chairs that meet safety, comfort, and durability standards tailored to their markets across Africa, South America, the Middle East, and Europe.
Related Video: Amazing factories | Manufacturing method and top 4 processes | Mass production process
Comprehensive Cost and Pricing Analysis for sensory Spinning chair Sourcing
Understanding the cost and pricing dynamics of sensory spinning chairs is essential for international B2B buyers aiming to optimize procurement strategies, especially when sourcing from diverse markets such as Africa, South America, the Middle East, and Europe. This section breaks down the key cost components, factors influencing pricing, and actionable buyer tips to navigate the complexities of this specialized product category.
Key Cost Components in Sensory Spinning Chair Manufacturing
-
Materials
The primary cost driver is the raw materials used, including high-quality plastics, metal frames (steel or aluminum), cushioning foams, and specialized sensory fabrics or finishes. Material selection impacts durability, comfort, and sensory effectiveness, with premium materials commanding higher prices. -
Labor
Skilled labor costs vary significantly by region. Countries with lower labor costs (e.g., Vietnam) can offer competitive pricing, whereas European manufacturers may price higher due to stringent labor regulations and higher wages, often justified by superior craftsmanship and quality controls. -
Manufacturing Overhead
This includes factory utilities, equipment depreciation, and indirect labor. Overhead costs are influenced by factory efficiency, automation level, and local economic conditions. -
Tooling and Setup
Initial investment in molds, dies, and tooling for mass production is significant. Higher tooling costs increase unit price but typically decrease with volume over time, benefiting large-scale buyers. -
Quality Control (QC)
Sensory spinning chairs often require rigorous QC to meet safety and comfort standards, including certifications for materials and mechanical safety. QC processes add to costs but ensure product reliability and reduce returns. -
Logistics and Shipping
Freight, customs duties, and insurance vary by shipment size, origin, and destination. For buyers in Africa or South America, sea freight is cost-effective but slower; air freight suits urgent orders but raises costs. Consider inland transport infrastructure quality, which can add to final landed costs. -
Supplier Margin
Manufacturer and distributor margins reflect market competition, product uniqueness, and service levels. Exclusive designs or patented features may carry premium pricing.
Price Influencers for Sensory Spinning Chairs
-
Order Volume and Minimum Order Quantity (MOQ)
Larger orders typically attract volume discounts, reducing per-unit cost. However, some manufacturers impose high MOQs that may not suit smaller businesses. -
Customization and Specifications
Custom colors, branding, or sensory features (e.g., specific fabric textures, compression levels) increase costs due to specialized production runs or materials. -
Material Quality and Certifications
Certified non-toxic materials, flame retardant fabrics, and ergonomic designs raise prices but are essential for compliance in many international markets, especially Europe. -
Supplier Reputation and Location
Established suppliers with a proven track record and compliance with international standards may price higher but offer reliability and reduced risk. -
Incoterms Selection
Terms like FOB, CIF, or DDP influence who bears logistics and customs costs. Buyers should understand these terms to accurately assess total purchase cost.
Strategic Tips for International B2B Buyers
-
Negotiate Beyond Unit Price
Engage suppliers on payment terms, shipping methods, and after-sales support to optimize overall deal value. -
Evaluate Total Cost of Ownership (TCO)
Consider not only purchase price but also shipping, customs duties, potential tariffs, storage, and warranty costs. For example, sourcing from Vietnam might offer lower production costs but higher shipping lead times and freight expenses. -
Leverage Local Market Knowledge
Buyers from Africa or South America should assess local import regulations and taxes that could significantly affect landed cost. Similarly, European buyers must verify compliance with EU safety standards, which can influence supplier selection and pricing. -
Request Samples and Certifications
Before committing to large orders, obtain product samples and verify certifications to mitigate risks related to quality and regulatory compliance. -
Monitor Currency Fluctuations
Exchange rate volatility can impact cost predictability. Consider forward contracts or local currency negotiations where feasible. -
Understand Pricing Nuances by Region
For example, Middle Eastern buyers often require customization aligned with cultural preferences, which can affect pricing. European buyers prioritize sustainability certifications, potentially increasing costs but enhancing marketability.
Indicative Pricing Disclaimer
Pricing for sensory spinning chairs varies widely based on the above factors. Indicative unit costs can range from approximately $50 to $300 or more, depending on material quality, customization, and order volume. Buyers should use this as a general guide and seek detailed quotations tailored to their specific requirements.
By thoroughly analyzing cost structures and pricing influencers, B2B buyers can make informed sourcing decisions that balance quality, compliance, and cost-efficiency in global sensory spinning chair procurement.
Spotlight on Potential sensory Spinning chair Manufacturers and Suppliers
This section looks at several manufacturers active in the ‘sensory Spinning chair’ market. This is a representative sample for illustrative purposes; B2B buyers must conduct extensive due diligence before any transaction. Information is synthesized from public sources and general industry knowledge.
Sensory Swivel Chairs Archives
Startinal specializes in manufacturing and supplying sensory spinning chairs alongside a diverse range of sensory training equipment, including balance toys, stepping stones, and scooter boards. Their product portfolio supports developmental and therapeutic needs, catering to educational and healthcare markets internationally, with a focus on quality and innovation for B2B buyers worldwide.
- 🌐 Domain: startinal.com
- 📅 Creation Year: 2016
- ⏳ Registered For: ~8.6 years
Autism Spinning Chair
Autism Spinning Chair specializes in therapeutic sensory spinning chairs designed to support children, teens, and adults with autism. Their products deliver controlled vestibular stimulation, aiding sensory regulation and body awareness. Built with durable, safety-focused materials, these chairs serve diverse settings including homes, schools, and therapy centers across global markets.
- 🌐 Domain: sensorychairs.com
- 📅 Creation Year: 2025
- ⏳ Registered For: ~0.5 years
Shop Sensory Spinning Seat
Shop Sensory Spinning Seat specializes in ergonomic sensory seating solutions designed to support focus and sensory regulation. Their product range includes innovative spinning seats tailored for neurodivergent users and active seating environments. Serving international B2B markets, they cater to educational, therapeutic, and commercial sectors seeking quality sensory furniture.
- 🌐 Domain: sensorydirect.com
- 📅 Creation Year: 2007
- ⏳ Registered For: ~18.1 years
Essential Technical Properties and Trade Terminology for sensory Spinning chair
Critical Technical Properties of Sensory Spinning Chairs
When sourcing sensory spinning chairs for international B2B trade, understanding key technical specifications is essential to ensure product quality, safety, and user satisfaction, especially given their specialized use for neurodivergent individuals.
-
Material Grade and Durability
Sensory spinning chairs are typically made from high-grade materials such as durable steel frames combined with fabric or leather upholstery. For B2B buyers, verifying the material grade (e.g., powder-coated steel, PU leather, or breathable mesh fabric) is crucial for durability and hygiene. High-quality materials ensure longer product lifespan, resistance to wear, and ease of cleaning—important factors for institutional buyers in schools, therapy centers, or offices. -
Weight Capacity and User Support
The maximum weight capacity (usually ranging from 100 kg to 150 kg or more) is a critical property. It guarantees safety and accommodates a broad user demographic, including adults and children. Buyers should confirm this spec aligns with their target users to avoid liability and returns. -
Rotational Mechanism and Stability
The spinning or swivel mechanism must offer smooth, controlled rotation with sufficient resistance to prevent accidental spins. This feature supports sensory stimulation without compromising user balance. Look for chairs with tested bearings or gas lift cylinders rated for stability and long-term use. -
Ergonomic Design and Sensory Features
Ergonomics tailored for sensory needs—such as contoured seats, adjustable heights, and cushioned supports—are vital. Some models incorporate compression seating or gentle rocking features to aid sensory regulation. These design elements enhance comfort and therapeutic efficacy, which is a major value proposition for buyers catering to neurodivergent populations. -
Tolerance and Quality Control Standards
Manufacturing tolerances (dimensional accuracy and assembly precision) affect chair safety and consistency. Chairs meeting ISO or EN safety standards demonstrate compliance with international regulations, reducing import risks and ensuring end-user protection. -
Surface Treatment and Finish
Surface treatments like anti-corrosion coating on metal parts and stain-resistant upholstery finishes are important for maintenance and durability in commercial settings. Buyers should inquire about certifications or tests related to surface quality to assess product longevity under heavy use.
Common Trade and Industry Terminology
Understanding common industry terms empowers B2B buyers to negotiate effectively and streamline procurement processes across regions like Africa, South America, the Middle East, and Europe.
-
OEM (Original Equipment Manufacturer)
Refers to manufacturers who produce chairs based on a buyer’s design or specifications. OEM partnerships allow buyers to customize sensory spinning chairs with specific materials, branding, or features, providing differentiation in competitive markets. -
MOQ (Minimum Order Quantity)
This is the smallest number of units a supplier will accept per order. MOQs vary widely depending on production scale and material costs. Buyers should balance MOQ requirements with inventory capacity and market demand to optimize cost-efficiency. -
RFQ (Request for Quotation)
A formal inquiry sent to suppliers asking for detailed pricing, lead times, and specifications. An RFQ is essential for comparing multiple sensory chair manufacturers and negotiating favorable terms. -
Incoterms (International Commercial Terms)
Standardized trade terms (e.g., FOB, CIF, EXW) that define the responsibilities and costs borne by buyers and sellers during shipping. Understanding Incoterms helps buyers manage logistics, customs duties, and delivery risks effectively. -
Lead Time
The period between order placement and product delivery. For sensory chairs, lead time impacts project timelines for schools or healthcare facilities. Buyers should clarify lead times upfront to avoid operational disruptions. -
Compliance Certification
Documentation proving the chair meets relevant safety and quality standards (e.g., CE marking in Europe). Certifications assure buyers of product legitimacy and reduce import clearance issues.
By focusing on these technical properties and trade terms, B2B buyers can make informed decisions when sourcing sensory spinning chairs, ensuring they procure products that meet user needs, comply with regional regulations, and align with business goals.
Navigating Market Dynamics, Sourcing Trends, and Sustainability in the sensory Spinning chair Sector
Market Overview & Key Trends
The sensory spinning chair sector is witnessing robust growth driven by increasing awareness of neurodiversity and the demand for ergonomic, therapeutic seating solutions globally. Key market drivers include rising diagnoses of sensory processing disorders, autism, ADHD, and a growing emphasis on inclusive environments in educational institutions and workplaces. For B2B buyers from regions such as Africa, South America, the Middle East, and Europe—including Vietnam and France—this translates into opportunities to meet the needs of diverse populations through specialized products that combine sensory stimulation with comfort and functionality.
Technological advancements are shaping product innovation, with manufacturers integrating adjustable features, multi-sensory feedback, and durable, easy-to-clean materials. The rise of active seating solutions like wobble stools, stability balls, and compression sensory chairs highlights a shift toward dynamic furniture that supports movement and self-regulation. For international buyers, sourcing trends emphasize customization capabilities and modular designs that cater to different age groups and therapeutic needs, enhancing product appeal across markets.
Market dynamics reveal a fragmented supply landscape with manufacturers ranging from specialized small enterprises to larger furniture producers expanding into the sensory segment. Africa and South America show growing demand driven by educational reforms and increasing investments in inclusive learning environments. Meanwhile, the Middle East and European markets prioritize premium quality and certification standards, reflecting higher regulatory scrutiny and consumer expectations. Vietnam serves as a competitive manufacturing hub offering cost-effective production with access to modern supply chains, appealing to global distributors seeking scalable sourcing options.
Sustainability & Ethical Sourcing in B2B
Sustainability in the sensory spinning chair sector is becoming a critical consideration for B2B buyers aiming to align procurement with global environmental goals and corporate social responsibility (CSR) mandates. The production of sensory chairs involves materials such as plastics, foams, textiles, and metals, which can carry significant environmental footprints if not responsibly sourced. Buyers are increasingly scrutinizing supply chains for eco-friendly practices, including the use of recycled or biodegradable materials, non-toxic finishes, and energy-efficient manufacturing processes.
Ethical sourcing extends beyond environmental concerns to encompass labor practices and supply chain transparency. Many regions, particularly in Africa and parts of South America, are encouraging partnerships with manufacturers who uphold fair labor standards and community development initiatives. Certifications such as GREENGUARD, FSC (Forest Stewardship Council) for wood components, and OEKO-TEX for textiles serve as important markers of sustainability and product safety, especially for buyers in Europe and the Middle East where regulatory frameworks emphasize green procurement.
Moreover, lifecycle considerations are gaining traction; B2B buyers favor suppliers offering products designed for durability and ease of repair or recycling. This approach not only reduces waste but also aligns with circular economy principles, increasingly demanded by institutional buyers such as schools and healthcare providers. Collaborating with manufacturers who provide transparent sustainability reporting and third-party audits can enhance buyer confidence and differentiate offerings in competitive markets.
Evolution and Historical Context
The concept of sensory seating originated from therapeutic needs to support individuals with neurodevelopmental conditions such as autism and ADHD. Early designs focused on simple active seating tools like stability balls and wobble stools to promote focus and physical engagement. Over time, these evolved into specialized sensory spinning chairs incorporating multi-sensory stimuli such as rocking, spinning, compression, and tactile feedback to address a broader range of sensory processing needs.
Historically, the market was niche, primarily driven by healthcare and special education sectors. However, growing awareness of sensory-friendly environments has expanded demand into mainstream education, offices, and residential markets. This evolution reflects a broader societal shift towards inclusivity and ergonomic wellness, transforming sensory spinning chairs from therapeutic aids into versatile furniture solutions. For B2B buyers, understanding this progression helps in evaluating product innovation and selecting suppliers aligned with contemporary user needs and regulatory requirements.
Frequently Asked Questions (FAQs) for B2B Buyers of sensory Spinning chair
-
How can I effectively vet sensory spinning chair suppliers from different regions such as Africa, South America, or Europe?
To vet suppliers, start by verifying their business licenses and certifications relevant to your target markets (e.g., CE for Europe). Request product samples to assess quality firsthand. Check references and customer reviews, especially from other international buyers. Use third-party inspection services to audit manufacturing capabilities and compliance with safety standards. Engage in direct communication to gauge responsiveness and transparency. Prioritize suppliers with experience in exporting to your region to minimize unforeseen trade barriers. -
What customization options are typically available for sensory spinning chairs, and how should I approach customization requests?
Most manufacturers offer options like adjustable seat sizes, different materials (fabric, leather, steel), colors, and added sensory features (compression zones, wobble functions). Clearly define your target user needs and intended applications before requesting custom features. Collaborate closely with suppliers to confirm feasibility, cost impact, and timelines. Always request prototypes or detailed design proofs before finalizing large orders to ensure the customization meets your quality and functional expectations. -
What are common minimum order quantities (MOQs) and lead times for sensory spinning chair manufacturing, especially for international buyers?
MOQs vary widely but typically range from 50 to 500 units depending on customization and supplier scale. Lead times generally span 4 to 12 weeks, influenced by order complexity and production capacity. For buyers in Africa, South America, or the Middle East, factor in additional time for shipping and customs clearance. Negotiating smaller MOQs or phased deliveries may be possible with some manufacturers, particularly for first orders, but expect slightly higher per-unit costs. -
Which payment terms are standard in international B2B transactions for sensory spinning chairs, and how can I protect my investment?
Common payment terms include 30% upfront deposit with balance paid upon shipment or after inspection. Letters of credit (LC) provide added security for both parties but require more documentation. Use escrow services or trade assurance platforms if available. Always confirm supplier banking details independently to avoid fraud. Insist on clear contract terms covering product specifications, delivery schedules, and penalties for non-compliance to safeguard your investment. -
What quality assurance certifications should I look for when sourcing sensory spinning chairs for global markets?
Look for ISO 9001 certification indicating a quality management system. CE marking is essential for the European market, ensuring compliance with health and safety standards. Depending on your region, additional certifications like RoHS (restriction of hazardous substances) or REACH compliance may be necessary. Request detailed product testing reports and material safety data sheets (MSDS) to verify adherence to international standards, which also facilitates smoother customs clearance. -
How can I optimize logistics and shipping for sensory spinning chair imports to regions like Africa or South America?
Work with freight forwarders experienced in your destination markets who can advise on cost-effective routes and modes (sea, air, or multimodal). Consolidate orders to reduce shipping costs per unit. Confirm packaging meets international standards to prevent damage during transit. Understand import duties, taxes, and customs documentation requirements to avoid delays. Establish clear communication channels with logistics partners for real-time shipment tracking and contingency planning. -
What strategies can help resolve disputes related to sensory spinning chair orders in international trade?
Include arbitration clauses in your purchase agreements specifying neutral venues and governing law. Maintain thorough documentation of all communications, contracts, and quality inspections. Use third-party inspection reports as impartial evidence in disputes. Attempt amicable resolution through direct negotiation before escalating. Engage trade associations or chambers of commerce in your region to mediate if necessary. Proactively managing expectations and clear contracts reduce dispute risks.
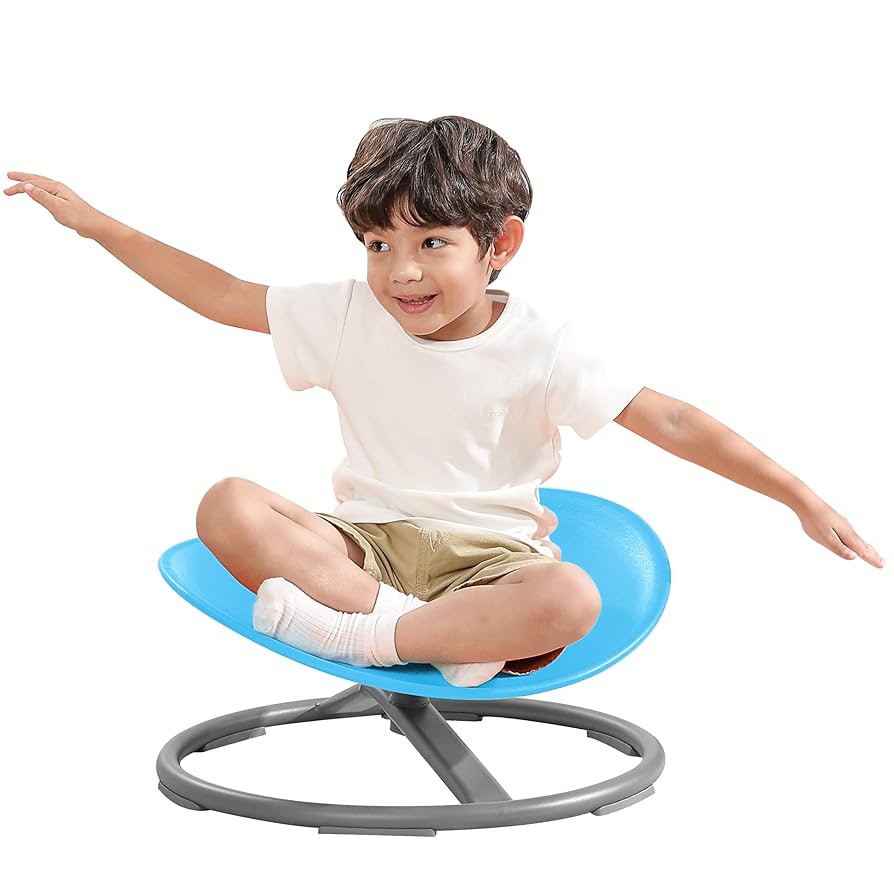
Illustrative Image (Source: Google Search)
- Are there specific considerations for sensory spinning chairs targeting neurodivergent users in international B2B sales?
Yes. Buyers should ensure that chairs meet ergonomic and sensory input requirements validated by occupational therapists or specialists familiar with autism and ADHD needs. Offering chairs with adjustable sensory features can appeal to diverse markets. Emphasize certifications and clinical testing data when marketing to healthcare or educational institutions. In regions with limited awareness, providing educational materials on benefits can support adoption and justify investment for institutional buyers.
Important Disclaimer & Terms of Use
⚠️ Important Disclaimer
The information provided in this guide, including content regarding manufacturers, technical specifications, and market analysis, is for informational and educational purposes only. It does not constitute professional procurement advice, financial advice, or legal advice.
While we have made every effort to ensure the accuracy and timeliness of the information, we are not responsible for any errors, omissions, or outdated information. Market conditions, company details, and technical standards are subject to change.
B2B buyers must conduct their own independent and thorough due diligence before making any purchasing decisions. This includes contacting suppliers directly, verifying certifications, requesting samples, and seeking professional consultation. The risk of relying on any information in this guide is borne solely by the reader.
Strategic Sourcing Conclusion and Outlook for sensory Spinning chair
Strategic Sourcing Insights and Future Directions for Sensory Spinning Chairs
As global demand for sensory spinning chairs rises—driven by increasing awareness of neurodiversity and ergonomic workplace solutions—international B2B buyers stand at a pivotal sourcing juncture. Key takeaways emphasize the importance of aligning product specifications with end-user sensory needs and prioritizing quality and adaptability to serve diverse markets across Africa, South America, the Middle East, and Europe. Buyers should focus on suppliers offering customizable designs, durable materials, and compliance with international safety standards to ensure broad usability and long-term value.
Strategic sourcing is essential to navigate this evolving market. Building partnerships with manufacturers who understand regional preferences and can support scalable production will mitigate risks associated with supply chain disruptions and fluctuating demand. Leveraging insights from market research and user feedback will enable buyers to optimize inventory and introduce innovative sensory seating solutions that enhance focus, comfort, and wellbeing in educational and professional environments.
Looking ahead, the sensory spinning chair market is poised for growth, propelled by rising investments in inclusive design and active seating solutions worldwide. B2B buyers from emerging and established markets are encouraged to proactively engage with manufacturers and distributors who demonstrate agility and a commitment to innovation. By adopting a strategic sourcing approach, buyers can secure competitive advantage while contributing to improved sensory experiences for neurodivergent and mainstream users alike.