Article Navigation
- Introduction: Navigating the Global Market for sensory room equipment for schools
- Understanding sensory room equipment for schools Types and Variations
- Key Industrial Applications of sensory room equipment for schools
- Strategic Material Selection Guide for sensory room equipment for schools
- In-depth Look: Manufacturing Processes and Quality Assurance for sensory room equipment for schools
- Comprehensive Cost and Pricing Analysis for sensory room equipment for schools Sourcing
- Spotlight on Potential sensory room equipment for schools Manufacturers and Suppliers
- Essential Technical Properties and Trade Terminology for sensory room equipment for schools
- Navigating Market Dynamics, Sourcing Trends, and Sustainability in the sensory room equipment for schools Sector
- Frequently Asked Questions (FAQs) for B2B Buyers of sensory room equipment for schools
- Important Disclaimer & Terms of Use
- Strategic Sourcing Conclusion and Outlook for sensory room equipment for schools
Introduction: Navigating the Global Market for sensory room equipment for schools
Sensory room equipment for schools has become an essential investment for educational institutions worldwide, addressing the growing recognition of sensory processing needs among students. These specialized environments support children with developmental, learning, and sensory integration challenges by providing calming, engaging, and therapeutic spaces that enhance focus, communication, and emotional regulation. For international B2B buyers—especially those operating in diverse markets such as Africa, South America, the Middle East, and Europe—sourcing the right sensory room equipment requires a nuanced understanding of product variety, quality standards, and regional market dynamics.
This comprehensive guide equips procurement professionals and institutional buyers with actionable insights to confidently navigate the global supply landscape. It covers critical aspects such as the different types of sensory equipment—including calming tools, active play installations, and specialized furniture—and the materials and manufacturing practices that ensure durability and safety. In addition, it delves into quality control benchmarks, supplier evaluation criteria, and cost considerations tailored to varied budget scales.
Moreover, the guide highlights regional sourcing opportunities and challenges, addressing logistics, compliance, and cultural preferences to optimize purchasing strategies. A detailed FAQ section further clarifies common concerns, helping buyers avoid pitfalls and leverage best practices. By synthesizing market intelligence and practical expertise, this resource empowers international buyers to make informed, strategic decisions that foster inclusive educational environments and maximize return on investment in sensory room infrastructure.
Understanding sensory room equipment for schools Types and Variations
Type Name | Key Distinguishing Features | Primary B2B Applications | Brief Pros & Cons for Buyers |
---|---|---|---|
Calming Sensory Equipment | Soft lighting, weighted blankets, soothing sounds | Special education classrooms, therapeutic centers | Pros: Enhances focus, reduces anxiety; Cons: May require electrical setup, moderate cost |
Active Sensory Equipment | Climbing structures, swings, ball pits | Physical therapy, motor skills development programs | Pros: Encourages movement, improves motor skills; Cons: Larger space needed, higher investment |
Interactive Sensory Toys | Fidget tools, tactile panels, cause-and-effect toys | Inclusive classrooms, occupational therapy | Pros: Portable, versatile; Cons: May require frequent replacement, small-scale impact |
Sensory Room Furniture | Soft seating, modular cushions, sensory mats | Multi-use sensory rooms, adaptable learning environments | Pros: Flexible configuration, durable; Cons: Bulkier, shipping logistics can be complex |
Visual & Auditory Systems | Projectors, bubble tubes, calming music systems | Autism support classrooms, special needs education | Pros: Multi-sensory engagement, customizable; Cons: Electrical dependency, maintenance needed |
Calming Sensory Equipment
This category includes items designed to create a tranquil environment, such as weighted blankets, soft LED lighting, and ambient sound machines. These are ideal for schools aiming to support students with anxiety, sensory processing disorders, or autism spectrum conditions. For B2B buyers, key considerations include the availability of electrical infrastructure and product certifications for safety. Investing in calming equipment can improve student focus and reduce behavioral incidents, but buyers should account for moderate pricing and ongoing maintenance.
Active Sensory Equipment
Active equipment promotes physical engagement through items like swings, climbing frames, and ball pits. These are best suited for physical therapy programs and schools focusing on motor skill development. B2B buyers must consider the spatial requirements and the durability of materials to withstand frequent use. While these installations often require a higher budget and adequate room size, they deliver significant benefits in physical coordination and sensory integration.
Interactive Sensory Toys
This type covers smaller, portable items such as fidget tools, tactile panels, and cause-and-effect toys that stimulate touch and cognitive skills. These are widely used in inclusive classrooms and occupational therapy settings. For international buyers, sourcing durable, easy-to-clean, and replaceable toys is crucial. Their portability and versatility make them cost-effective, though they might need frequent replenishment due to wear or loss.
Sensory Room Furniture
Furniture designed specifically for sensory rooms includes modular cushions, soft seating, and mats that can be arranged to create safe, adaptable spaces. This furniture supports both calming and active sensory activities and is essential for multi-functional sensory rooms. Buyers should evaluate the quality of materials for hygiene and durability, as well as logistical factors like shipping costs and assembly requirements, especially in regions with complex import regulations.
Visual & Auditory Systems
These systems encompass bubble tubes, projectors, and sound machines that engage visual and auditory senses. They are particularly effective in classrooms for children with autism or sensory processing challenges. B2B buyers should ensure compatibility with local electrical standards and consider installation support. Although these systems involve higher upfront costs and maintenance, they offer customizable sensory experiences that enhance learning and emotional regulation.
Related Video: The Attention Mechanism in Large Language Models
Key Industrial Applications of sensory room equipment for schools
Industry/Sector | Specific Application of sensory room equipment for schools | Value/Benefit for the Business | Key Sourcing Considerations for this Application |
---|---|---|---|
Education & Special Needs | Creating therapeutic sensory rooms to support neurodiverse and special needs students | Enhances learning outcomes, supports behavioral management, and improves inclusion | Durable, safe materials; culturally adaptable designs; compliance with local safety standards; easy maintenance |
Healthcare & Therapy | Integrating sensory equipment in school-based occupational therapy programs | Facilitates sensory integration therapy, accelerates developmental milestones | Equipment certified for therapeutic use; adjustable sensory stimuli; availability of replacement parts |
Educational Technology | Incorporating interactive sensory tools for cognitive and motor skill development | Boosts engagement, supports individualized learning plans, and tracks progress | Compatibility with existing tech infrastructure; multilingual instructions; robust technical support |
Government & Public Sector | Equipping public schools with sensory rooms to comply with inclusive education policies | Meets regulatory requirements, promotes equal access, and enhances community wellbeing | Cost-effectiveness; scalability for multiple schools; compliance with public procurement rules |
Non-Profit & NGOs | Deploying sensory rooms in schools within underserved regions | Provides critical support to vulnerable children, improves social-emotional skills | Portable, easy-to-install equipment; low power consumption; culturally sensitive design |
Education & Special Needs
Sensory room equipment in the education sector is primarily used to create therapeutic environments tailored to neurodiverse and special needs students, including those with autism spectrum disorders and sensory processing challenges. These rooms help reduce anxiety, improve focus, and foster better behavioral regulation. For international buyers, especially from regions like Africa and South America where inclusive education is expanding, sourcing equipment that meets stringent safety standards and is adaptable to various cultural contexts is crucial. Durability and ease of maintenance are also key to ensure longevity in diverse climates.
Healthcare & Therapy
Occupational therapists in schools utilize sensory room equipment to deliver sensory integration therapy that aids children with developmental delays and physical disabilities. This equipment supports motor skills, balance, and sensory processing improvements. Buyers from the Middle East and Europe should prioritize equipment certified for therapeutic use, with adjustable sensory inputs to tailor sessions to individual needs. Availability of spare parts and after-sales support is essential to maintain continuity in therapy programs.
Educational Technology
Interactive sensory tools integrated into classrooms enhance cognitive and motor skill development through engaging, multisensory learning experiences. These tools assist teachers in personalizing education and monitoring student progress. For B2B buyers in technologically advancing markets like Poland and Indonesia, compatibility with existing educational technology infrastructure and multilingual user manuals are vital. Robust technical support and warranty services also ensure sustained usage and reduce downtime.
Government & Public Sector
Public education authorities increasingly mandate inclusive education facilities that accommodate children with sensory needs. Equipping public schools with sensory rooms helps meet these legal requirements while promoting social equity and community wellbeing. Buyers in this sector should focus on cost-effective, scalable solutions that can be deployed across multiple schools. Compliance with public procurement regulations and local safety certifications are also critical to ensure smooth acquisition and implementation.
Non-Profit & NGOs
Non-governmental organizations working in underserved or remote regions use sensory room equipment to support vulnerable children’s social-emotional development and learning. Equipment designed for portability and easy installation is advantageous, as is low power consumption due to potential infrastructure limitations. Additionally, culturally sensitive designs that respect local norms and preferences improve acceptance and effective use of sensory rooms in diverse communities across Africa, South America, and other regions.
Related Video: The Sensory Room: Helping Students With Autism Focus and Learn
Strategic Material Selection Guide for sensory room equipment for schools
High-Density Polyethylene (HDPE)
Key Properties:
HDPE is a thermoplastic known for its excellent impact resistance, chemical inertness, and moisture resistance. It withstands a wide temperature range (-100°C to 120°C) and exhibits strong corrosion resistance, making it suitable for long-term use in various environments.
Pros & Cons:
HDPE is highly durable and resistant to cracking or warping, which is essential for frequently handled sensory room equipment like tactile panels or interactive toys. It is cost-effective and relatively easy to manufacture via molding processes. However, it has limited UV resistance unless treated, which can be a concern for rooms with natural light exposure. Additionally, HDPE’s surface can be difficult to bond with adhesives, requiring mechanical fasteners or special coatings.
Impact on Application:
Due to its non-toxic nature and ease of cleaning, HDPE is ideal for sensory toys, panels, and furniture surfaces that require frequent sanitation. Its resistance to moisture and chemicals makes it suitable for multi-use environments like schools in humid climates common in parts of Africa and South America.
International B2B Considerations:
Buyers in Europe and the Middle East should ensure HDPE products comply with ASTM D4976 or EN 14214 standards for material safety and recyclability. In regions like Indonesia and Poland, local certifications on food-grade or medical-grade plastics may be relevant if equipment contacts skin extensively. HDPE sourced from suppliers with ISO 9001 certification ensures consistent quality, which is critical for institutional buyers.
Polyvinyl Chloride (PVC) – Soft and Rigid Forms
Key Properties:
PVC offers versatility in sensory room equipment, available in both rigid and flexible forms. It is chemically resistant, flame retardant, and has good dimensional stability. Soft PVC variants provide cushioning and tactile feedback, while rigid PVC is structurally robust.
Pros & Cons:
PVC’s flexibility in form allows manufacturers to create a wide range of sensory products, from soft mats to sturdy frames. It is cost-effective and widely available globally. However, PVC can release harmful phthalates unless carefully formulated, which raises health concerns. It also has moderate resistance to UV and may degrade under prolonged sunlight exposure, requiring additives for stabilization.
Impact on Application:
Soft PVC is excellent for calming sensory mats or chewable items, providing safe tactile stimulation. Rigid PVC can be used for frames and structural elements in sensory furniture. Its flame retardancy is a significant advantage for compliance with school safety regulations.
International B2B Considerations:
Buyers in Africa and South America should verify compliance with international safety standards such as REACH (Europe) or local equivalents to avoid harmful plasticizers. Middle Eastern buyers may prioritize flame retardancy certifications (e.g., UL 94 V-0 rating). Sourcing PVC that meets ISO 14001 environmental management standards can also be a selling point in Europe and Indonesia, where sustainability is increasingly valued.
Natural Rubber and Silicone Rubber
Key Properties:
Natural rubber and silicone rubber provide excellent elasticity, tactile softness, and durability. Silicone rubber stands out for its high thermal stability (-60°C to 230°C), chemical inertness, and hypoallergenic properties, making it ideal for sensitive users.
Pros & Cons:
Rubber materials offer superior sensory feedback through touch and flexibility, essential for fidget tools, grips, and soft swings. Silicone rubber is more expensive but offers longer life and better resistance to environmental factors than natural rubber, which can degrade with UV exposure and ozone. Both materials require specialized manufacturing processes like molding or extrusion.
Impact on Application:
Rubber materials are preferred for equipment requiring flexibility and cushioning, such as swings, stress balls, and chewable sensory aids. Silicone’s hypoallergenic nature is particularly important for users with skin sensitivities, common among children with sensory processing disorders.
International B2B Considerations:
For buyers in Europe and the Middle East, compliance with FDA or EU food-contact regulations is critical when rubber products contact skin or mouths. In Africa and South America, availability of medical-grade silicone may be limited; hence, buyers should verify supplier certifications such as ISO 10993 for biocompatibility. Cost and supply chain reliability are key considerations in Indonesia and Poland due to fluctuating import tariffs and local manufacturing capabilities.
Upholstery-Grade Foam (Polyurethane Foam)
Key Properties:
Polyurethane foam is lightweight, compressible, and available in various densities and firmness levels. It offers excellent shock absorption and cushioning, essential for comfort and safety in sensory room seating and mats.
Pros & Cons:
Foam is cost-effective and easy to shape, making it suitable for custom sensory furniture and floor mats. It provides good thermal insulation and noise dampening. However, polyurethane foam is flammable unless treated and can degrade over time with exposure to moisture and UV light. It may also emit volatile organic compounds (VOCs) if not properly manufactured.
Impact on Application:
Foam is ideal for calming areas where soft seating or padded surfaces reduce sensory overload. It supports safe physical interaction and helps prevent injuries. Treated flame retardant foam aligns with school safety codes in many countries.
International B2B Considerations:
Buyers from Europe and the Middle East should require compliance with EN 597 (flammability) and OEKO-TEX standards for chemical safety. In African and South American markets, sourcing foam with certifications for low VOC emissions is important due to indoor air quality concerns. For Indonesia and Poland, local fire safety regulations may dictate specific foam grades or treatments.
Material | Typical Use Case for sensory room equipment for schools | Key Advantage | Key Disadvantage/Limitation | Relative Cost (Low/Med/High) |
---|---|---|---|---|
High-Density Polyethylene (HDPE) | Tactile panels, interactive toys, furniture surfaces | Durable, moisture and chemical resistant, easy to clean | Limited UV resistance, bonding challenges | Low |
Polyvinyl Chloride (PVC) | Soft mats, chewable items, structural frames | Versatile (soft and rigid), flame retardant | Potentially harmful plasticizers, moderate UV resistance | Low |
Natural & Silicone Rubber | Fidget tools, swings, chewable sensory aids | Excellent elasticity, hypoallergenic (silicone) | Natural rubber degrades with UV; silicone is costly | Medium |
Upholstery-Grade Foam | Soft seating, padded mats, calming areas | Lightweight, shock-absorbing, customizable | Flammable unless treated, potential VOC emissions | Low to Medium |
In-depth Look: Manufacturing Processes and Quality Assurance for sensory room equipment for schools
Manufacturing sensory room equipment for schools involves a meticulous process that ensures safety, durability, and therapeutic efficacy. For international B2B buyers—especially those sourcing from or supplying to regions like Africa, South America, the Middle East, and Europe—understanding these manufacturing stages and quality assurance protocols is critical for selecting reliable partners and ensuring compliance with regional standards.
Typical Manufacturing Process for Sensory Room Equipment
The production of sensory room equipment spans several core stages, each demanding specialized techniques tailored to the unique functional and safety requirements of educational environments.
1. Material Preparation
- Selection of Raw Materials: Manufacturers prioritize non-toxic, hypoallergenic, and durable materials such as high-density foam, medical-grade plastics, treated wood, and soft fabrics. Material sourcing often includes certifications for child safety and environmental compliance.
- Pre-treatment: Materials undergo processes like sterilization, anti-microbial treatment, flame retardant application, or UV stabilization, depending on the product type and intended use environment.
2. Forming and Fabrication
- Cutting and Shaping: CNC machines, laser cutters, and die-cutting tools are commonly used for precision shaping of components like foam panels, plastic parts, and wooden frames.
- Molding: For plastic or rubber components (e.g., tactile toys, swings), injection molding or rotational molding techniques ensure consistent shape and texture.
- Sewing and Upholstery: Fabrics and covers are tailored using industrial sewing machines, often incorporating removable, washable covers for hygiene.
3. Assembly
- Component Integration: Assembly lines combine fabricated parts with hardware such as fasteners, hinges, and electronic components (e.g., LED lighting, sound modules).
- Electrical Wiring: For interactive or sensory technology products, certified electricians integrate wiring harnesses with safety features like insulated connectors and circuit breakers.
- Modular Assembly: Many products use modular designs to facilitate transportation and customization, critical for international shipping and diverse school environments.
4. Finishing and Packaging
- Surface Treatment: Surfaces receive protective coatings—such as anti-scratch, waterproof, or anti-microbial finishes—to enhance longevity and safety.
- Labeling: Products are labeled with safety warnings, usage instructions, and certification marks in multiple languages as per export requirements.
- Packaging: Robust packaging solutions, often with impact-absorbing materials, are used to protect sensitive equipment during international transit.
Quality Assurance and Control (QA/QC) in Sensory Room Equipment Production
Robust quality assurance frameworks are essential to ensure sensory room equipment meets international safety, performance, and durability standards.
Relevant International and Industry Standards
- ISO 9001: The cornerstone quality management system standard applicable to manufacturers, ensuring consistent production and continual improvement.
- CE Marking: Mandatory for products sold within the European Economic Area (EEA), indicating conformity with health, safety, and environmental protection standards.
- ASTM and EN Standards: Specific standards such as ASTM F963 (toy safety) and EN 71 (safety of toys) are relevant for many sensory toys and equipment.
- RoHS and REACH Compliance: Ensures hazardous substances are restricted, critical for European and Middle Eastern markets.
- Electrical Safety Certifications: IEC 60601 (medical electrical equipment) or equivalent local standards apply for electrically powered sensory devices.
- Local Certifications: Buyers from regions such as Africa or South America should verify compliance with regional regulatory bodies or import requirements (e.g., INMETRO in Brazil).
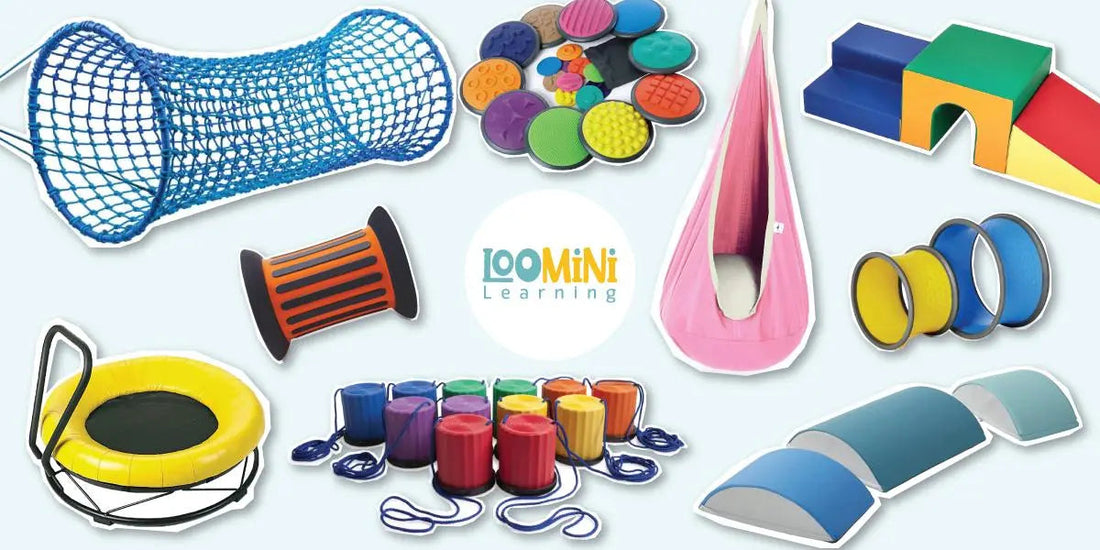
Illustrative Image (Source: Google Search)
Key QC Checkpoints Across Production Stages
- Incoming Quality Control (IQC): Inspection and testing of raw materials for defects, chemical safety, and compliance certificates before acceptance.
- In-Process Quality Control (IPQC): Continuous monitoring during forming, assembly, and finishing stages to detect deviations such as dimensional inaccuracies, improper assembly, or faulty wiring.
- Final Quality Control (FQC): Comprehensive testing of finished products including mechanical strength, functionality, safety features, and aesthetic inspections before packaging.
Common Testing Methods
- Mechanical Testing: Load-bearing capacity tests, impact resistance, and durability assessments simulate real-world use conditions.
- Chemical Testing: Verification of non-toxicity, absence of harmful phthalates, lead, or other restricted substances.
- Electrical Safety Testing: Insulation resistance, leakage current, and grounding continuity tests for powered devices.
- Functional Testing: Validation of sensory outputs like sound, light, vibration, and tactile feedback meet design specifications.
- Hygiene Testing: Anti-microbial efficacy and ease of cleaning are verified, particularly for soft furnishings and fabrics.
Verifying Supplier Quality: Practical Steps for B2B Buyers
For international buyers, especially those operating in markets with diverse regulatory frameworks, due diligence in supplier quality verification is crucial.
- Factory Audits: Conduct on-site or third-party audits focusing on production capabilities, quality management systems (e.g., ISO 9001 certification), and compliance with safety standards.
- Review of Quality Documentation: Request and analyze quality control plans, material certificates, test reports, and calibration records.
- Third-Party Inspections: Employ independent inspection agencies for pre-shipment verification to check conformity, packaging integrity, and labeling accuracy.
- Sample Testing: Obtain product samples for lab testing in accredited facilities in the buyer’s country or region to validate compliance with local regulations.
- Supplier Transparency: Engage suppliers who provide traceability of materials and components, and who demonstrate responsiveness to quality issues and corrective actions.
QC and Certification Nuances for International Markets
- Africa: Regulatory frameworks vary widely; buyers should prioritize suppliers with international certifications (ISO, CE) and conduct local compliance checks, especially for electrical products.
- South America: Countries like Brazil require INMETRO certification; buyers must ensure suppliers can provide appropriate documentation and meet import standards.
- Middle East: Compliance with GCC Standardization Organization (GSO) and local electrical safety requirements is critical; certification for flame retardancy and hygiene is often emphasized.
- Europe (e.g., Poland): CE marking and compliance with EU directives are mandatory; buyers should confirm that sensory equipment meets EN standards and environmental regulations like REACH.
- Cross-Regional Considerations: Language localization on labels and manuals, compatibility with local electrical voltage/frequency, and cultural suitability of sensory stimuli should be addressed by manufacturers.
Conclusion
For B2B buyers investing in sensory room equipment for schools, a deep understanding of manufacturing processes and stringent quality assurance practices is vital. Prioritizing suppliers with transparent, standardized manufacturing workflows and comprehensive QC systems—backed by internationally recognized certifications—ensures the delivery of safe, effective, and compliant sensory products. This approach minimizes risks, facilitates smoother importation, and ultimately supports the creation of nurturing sensory environments tailored to diverse educational needs worldwide.
Related Video: SMART Quality Control for Manufacturing
Comprehensive Cost and Pricing Analysis for sensory room equipment for schools Sourcing
Understanding the cost and pricing landscape of sensory room equipment for schools is crucial for international B2B buyers aiming to make informed procurement decisions. This analysis breaks down the core cost components, key price influencers, and practical buyer strategies, especially tailored for markets in Africa, South America, the Middle East, and Europe.
Core Cost Components
-
Materials
The primary cost driver is the quality and type of materials used—ranging from durable plastics, soft textiles, sensory-safe foam, to electronic components for interactive devices. High-grade, hypoallergenic, and certified non-toxic materials typically command premium pricing but ensure safety and longevity in school environments. -
Labor and Manufacturing Overhead
Labor costs vary widely depending on the manufacturing location and complexity of assembly. Skilled labor for producing customizable or electronically integrated sensory equipment can elevate costs. Overhead includes factory utilities, equipment depreciation, and administrative expenses. -
Tooling and Customization
Initial tooling for molds or bespoke parts adds upfront costs, especially for specialized sensory furniture or custom-designed equipment. Buyers seeking tailored solutions should anticipate higher unit prices at lower volumes due to tooling amortization. -
Quality Control (QC)
Rigorous QC processes—such as safety testing, certifications (e.g., CE marking, ASTM standards)—add costs but are critical for compliance and user safety. Certified equipment often involves higher inspection and testing fees that influence final pricing. -
Logistics and Import Costs
Freight, insurance, customs duties, and handling fees can significantly affect landed costs. Sensory room equipment can be bulky or delicate, requiring specialized packaging and shipping methods, which may increase logistics expenses. -
Supplier Margin
Suppliers incorporate margins that reflect market conditions, brand positioning, and service levels. Margins vary widely between manufacturers, distributors, and agents, especially when dealing with international trade.
Key Price Influencers
-
Order Volume and Minimum Order Quantities (MOQ)
Larger orders typically unlock volume discounts and reduce per-unit costs. However, smaller institutions or regional buyers may face higher costs due to MOQ constraints. -
Specifications and Customization
Equipment with advanced sensory features (e.g., multi-sensory lighting, adaptive swings) or custom branding/design will attract price premiums. Standardized products generally cost less but may offer limited adaptability. -
Material Quality and Certifications
Products meeting international safety and quality certifications (ISO, CE, RoHS) command higher prices but reduce risk and liability. -
Supplier Location and Reputation
Established suppliers with proven track records and reliable after-sales support may price higher but provide greater assurance. Conversely, emerging manufacturers in Asia or Eastern Europe might offer competitive pricing with variable quality. -
Incoterms and Payment Terms
The choice of Incoterms (e.g., FOB, CIF, DDP) affects who bears freight and insurance costs, influencing total landed price. Favorable payment terms (letters of credit, net 30/60) can improve cash flow and negotiation leverage.
Buyer Tips for Cost Efficiency and Negotiation
-
Conduct Total Cost of Ownership (TCO) Analysis
Evaluate not only the purchase price but also shipping, installation, maintenance, and expected lifespan. Investing in durable, certified equipment can reduce long-term replacement and downtime costs. -
Negotiate Volume-Based Discounts and Flexible MOQs
Buyers from smaller markets (e.g., African or South American schools) should negotiate flexible MOQs or pooled purchases with other institutions to achieve better pricing. -
Leverage Regional Trade Agreements and Logistics Hubs
Utilize free trade agreements (e.g., African Continental Free Trade Area, EU trade policies) to minimize tariffs. Consider sourcing from regional suppliers or logistics hubs (e.g., Poland for Europe, UAE for Middle East) to reduce transit times and costs. -
Request Samples and Certification Documentation
Prioritize suppliers who provide product samples and transparent certification evidence to ensure compliance with local safety standards. -
Consider Modular or Scalable Equipment
Phased procurement of sensory equipment allows spreading costs over time and adapting to budget constraints without compromising quality. -
Be Mindful of Currency Fluctuations and Payment Methods
Currency volatility can affect final costs; locking exchange rates or using hedging instruments may protect budgets. Payment methods that build supplier trust can open doors for better pricing.
Indicative Pricing Disclaimer
Prices for sensory room equipment vary widely based on product complexity, customization, and supplier region. For example, basic sensory toys and calming tools may start from USD 20–100 per unit, whereas specialized furniture or electronic sensory panels can range from USD 500 to several thousand per piece. Buyers should request detailed quotations and consider all cost factors before finalizing orders.
By understanding these cost drivers and pricing influences, international B2B buyers can optimize procurement strategies, ensuring quality sensory room setups that meet educational needs while respecting budgetary and logistical realities.
Spotlight on Potential sensory room equipment for schools Manufacturers and Suppliers
This section looks at several manufacturers active in the ‘sensory room equipment for schools’ market. This is a representative sample for illustrative purposes; B2B buyers must conduct extensive due diligence before any transaction. Information is synthesized from public sources and general industry knowledge.
Experia USA
Experia USA specializes in high-quality sensory room equipment designed to enhance learning environments in schools. Their product range includes bubble tubes, sensory fiber optics, projectors, soft play, and tactile accessories, catering to diverse sensory needs. With free shipping across 48 states and a UK presence, they serve international B2B buyers seeking innovative sensory solutions.
- 🌐 Domain: experia-usa.com
- 📅 Creation Year: 2009
- ⏳ Registered For: ~16.0 years
Sensory Room Equipment (OT Recommendations)
Detailed public information about this company is limited. It is recommended to visit their website directly for inquiries.
- 🌐 Domain: theottoolbox.com
- 📅 Creation Year: 2017
- ⏳ Registered For: ~8.5 years
Sensory Room Equipment
Detailed public information about this company is limited. It is recommended to visit their website directly for inquiries.
- 🌐 Domain: funandfunction.com
- 📅 Creation Year: 2005
- ⏳ Registered For: ~19.9 years
Essential Technical Properties and Trade Terminology for sensory room equipment for schools
Critical Technical Properties of Sensory Room Equipment
-
Material Grade and Safety Compliance
Sensory room equipment must use non-toxic, hypoallergenic, and durable materials—often medical-grade plastics, soft foam with fire-retardant covers, or BPA-free silicone. Compliance with international safety standards (e.g., EN71 for toys in Europe, ASTM F963 in the US) is crucial. For B2B buyers, verifying material certifications reduces liability risks and ensures equipment longevity under frequent use by children. -
Weight and Load Tolerance
Products such as swings, therapy balls, and climbing structures specify maximum load capacities. These tolerances must account for diverse user weights and safety margins. Buyers should request detailed load ratings and stress-test certifications to ensure equipment durability and safe use in school environments with mixed-age groups. -
Sensory Modality Specifications
Equipment is designed to stimulate specific senses: tactile (texture types), visual (light intensity and color range), auditory (sound volume and frequency), and proprioceptive (pressure levels). Technical specs on light wavelength, decibel limits, or vibration frequency help buyers match products to users’ sensory needs and avoid overstimulation or under-stimulation. -
Dimensional Accuracy and Space Requirements
Precise dimensions, including height, footprint, and clearance space, are vital for fitting equipment into existing rooms while ensuring safe user movement. Tolerances in manufacturing affect installation and user accessibility. B2B buyers should request detailed CAD drawings or dimensional datasheets to plan room layouts efficiently. -
Electrical and Power Specifications
For interactive or electronic sensory equipment (e.g., bubble tubes, sound systems), voltage, power consumption, and plug type compatibility (e.g., 220V/50Hz for Europe, 110V/60Hz for the Americas) must be clearly stated. Buyers in diverse regions must verify these specs to avoid costly modifications or non-compliance with local electrical codes. -
Maintenance and Durability Standards
Equipment designed for schools should offer easy cleaning protocols (e.g., wipeable surfaces, water resistance) and robust construction to withstand frequent use. Spec sheets often include expected lifespan and warranty terms. B2B buyers should prioritize products with clear maintenance guidelines to minimize downtime and replacement costs.
Key Trade Terminology for Sensory Room Equipment Procurement
-
OEM (Original Equipment Manufacturer)
Refers to companies that produce sensory room equipment components or entire products that may be branded and sold by another company. Understanding OEM relationships helps buyers negotiate customization options and pricing, especially when sourcing bulk or private-label products. -
MOQ (Minimum Order Quantity)
The smallest quantity a supplier is willing to sell in one order. MOQs can impact procurement strategy and budgeting, particularly for smaller schools or pilot projects. International buyers should clarify MOQ to balance inventory costs and meet demand. -
RFQ (Request for Quotation)
A formal document sent to suppliers asking for detailed pricing, delivery, and product specifications. RFQs are essential for comparing offers from multiple vendors, ensuring transparency and competitive pricing in B2B transactions. -
Incoterms (International Commercial Terms)
Standardized trade terms defining responsibilities and risks between buyers and sellers during shipment (e.g., FOB, CIF, DDP). Understanding Incoterms helps international buyers from Africa, South America, the Middle East, and Europe negotiate delivery costs, customs clearance, and liability effectively. -
Lead Time
The period between placing an order and receiving the goods. Lead times vary depending on production complexity and shipping distance. B2B buyers must factor lead times into project planning to avoid delays in setting up sensory rooms. -
Certification and Compliance Documentation
Includes product safety certificates, material test reports, and conformity declarations. These documents are often mandatory for import clearance and institutional procurement. Requesting these upfront safeguards buyers against regulatory issues and ensures product safety.
By focusing on these technical specifications and trade terms, international B2B buyers can make well-informed purchasing decisions that align with their educational goals, budget constraints, and regulatory environments. This approach minimizes risks, optimizes resource allocation, and ultimately supports the successful implementation of sensory rooms in diverse school settings worldwide.
Navigating Market Dynamics, Sourcing Trends, and Sustainability in the sensory room equipment for schools Sector
Market Overview & Key Trends
The global market for sensory room equipment tailored to educational institutions is witnessing steady growth, driven by increased awareness of neurodiversity and the rising demand for inclusive learning environments. Schools worldwide, particularly in Africa, South America, the Middle East, and Europe, are investing in sensory rooms to support students with autism spectrum disorders, sensory processing challenges, and other developmental needs. This shift is propelled by government initiatives promoting special education and growing parental advocacy for tailored learning solutions.
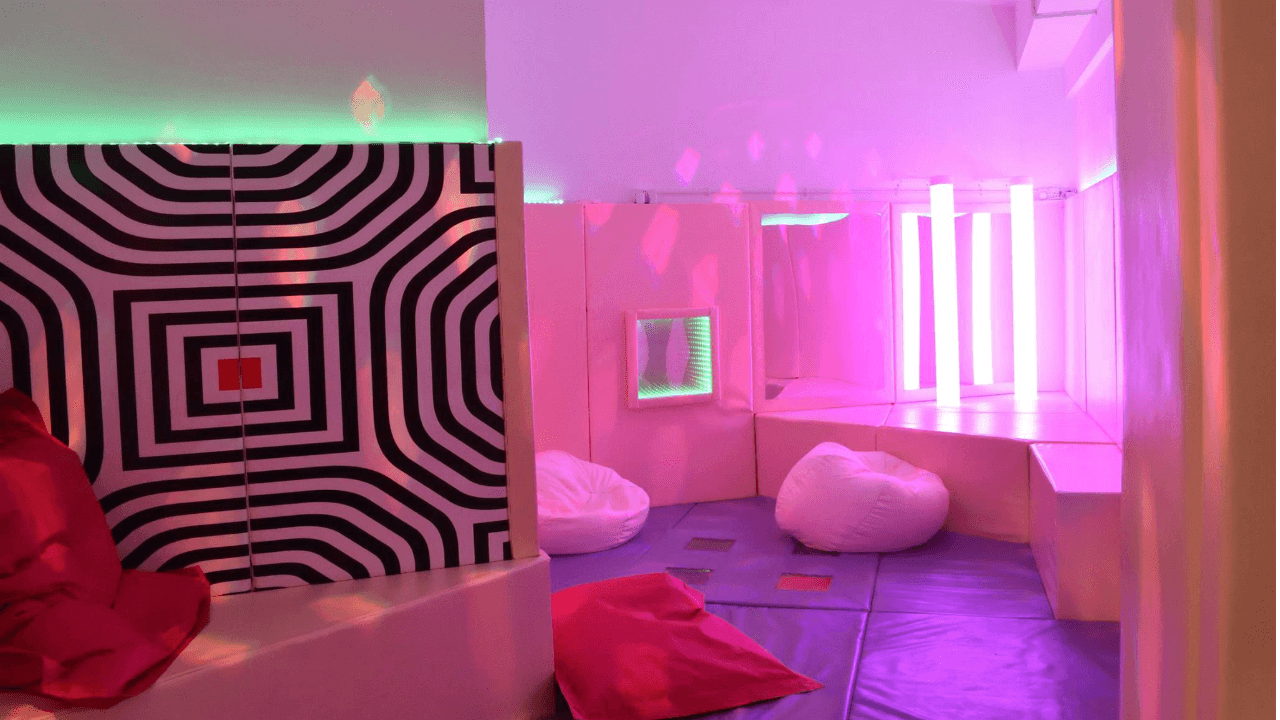
Illustrative Image (Source: Google Search)
Key market dynamics include diversification of product offerings, with suppliers expanding beyond traditional sensory toys to integrate technology-enabled equipment such as interactive lighting, sound systems, and adaptive furniture. Buyers from emerging economies like Indonesia and Brazil are increasingly looking for modular, scalable sensory room solutions that can be adapted to varying classroom sizes and budgets. European buyers, notably from countries like Poland, prioritize compliance with stringent safety and educational standards, influencing procurement decisions and driving demand for certified products.
B2B sourcing trends emphasize the need for suppliers with robust global logistics capabilities and customizable product portfolios. Digital platforms facilitating virtual product demos and detailed specification sharing are becoming essential tools for international buyers managing complex procurement processes remotely. Additionally, the rise of hybrid sensory environments—combining physical equipment with digital sensory input devices—is an emerging trend that enhances engagement and learning outcomes.
For international buyers, understanding regional regulatory frameworks and cultural nuances is critical. For instance, Middle Eastern markets may favor sensory equipment that aligns with local educational policies and cultural sensitivities, while African buyers often seek cost-effective yet durable products that withstand varied climatic conditions.
Sustainability & Ethical Sourcing in B2B
Sustainability is an increasingly pivotal factor in the procurement of sensory room equipment for schools. International buyers are prioritizing suppliers that demonstrate commitment to environmental stewardship through responsible material sourcing, production processes, and end-of-life product management. Given the educational sector’s focus on long-term impact, eco-friendly sensory products—such as those made from sustainably harvested wood, recycled plastics, and non-toxic, hypoallergenic materials—are gaining traction.
Ethical supply chains are equally important, ensuring that manufacturing partners adhere to fair labor practices and avoid exploitative conditions. Certifications like FSC (Forest Stewardship Council) for wood products, OEKO-TEX for textiles, and ISO 14001 for environmental management systems are increasingly demanded by buyers in Europe and the Middle East. These certifications provide assurance of compliance with environmental and social governance (ESG) criteria, enhancing the reputation of schools as responsible institutions.
In addition to materials, energy-efficient production and logistics play a role in reducing the carbon footprint associated with sensory room equipment. Buyers are encouraged to engage suppliers who optimize packaging to minimize waste and who offer take-back or recycling programs for obsolete or damaged equipment. This approach aligns with global sustainability goals and fosters circular economy principles within the educational supply chain.
Brief Evolution and Historical Context
Sensory rooms originated in the late 20th century as therapeutic spaces primarily designed for individuals with autism and sensory processing disorders. Initially, these rooms featured basic calming tools like weighted blankets, soft lighting, and tactile toys. Over time, the concept evolved from specialized therapy centers to mainstream educational settings, reflecting a broader understanding of diverse learning needs.
The historical shift towards inclusive education policies worldwide accelerated the adoption of sensory rooms in schools, especially in developed regions. Advances in adaptive technology and increased research into sensory integration therapy have enriched the product landscape, enabling suppliers to offer more sophisticated, evidence-based equipment. Today, sensory rooms are recognized not only as therapeutic environments but also as essential educational tools that support cognitive development, emotional regulation, and social skills in students across varied cultural contexts. This evolution underscores the importance for B2B buyers to stay abreast of innovations and evolving standards to make informed procurement decisions.
Related Video: Global Trends Tutorial: Chapter 3: IPE
Frequently Asked Questions (FAQs) for B2B Buyers of sensory room equipment for schools
-
How can I effectively vet international suppliers of sensory room equipment to ensure reliability and quality?
Begin by verifying the supplier’s business credentials, such as registration certificates and export licenses. Request product samples and detailed technical specifications to assess quality firsthand. Check references or customer testimonials, especially from other schools or institutions in your region. Utilize third-party inspection services or audits to validate manufacturing standards. Additionally, confirm the supplier’s experience with international shipping and compliance with import regulations relevant to your country to avoid customs delays. -
Is customization of sensory room equipment available, and how do I manage specifications across different markets?
Many manufacturers offer customization options, including size, materials, colors, and sensory features tailored to specific educational or therapeutic needs. Clearly communicate your requirements in writing, supported by drawings or product references. Understand local regulations or standards that may affect design or materials (e.g., fire safety or non-toxic certifications). Negotiate minimum order quantities (MOQs) for custom items, as they may differ from standard products. Establish a prototype approval process before mass production to minimize costly revisions. -
What are typical minimum order quantities (MOQs), lead times, and payment terms I should expect when sourcing sensory room equipment internationally?
MOQs vary widely depending on product type and customization level; bulk furniture items often require higher MOQs than smaller sensory toys. Lead times generally range from 4 to 12 weeks, influenced by production complexity and shipping method. Payment terms commonly include a 30%-50% deposit upfront, with the balance paid before shipment or upon delivery, often via Letter of Credit or secure wire transfer. Negotiate terms carefully, considering currency risks and banking regulations in your country. -
Which quality assurance certifications should I look for to ensure sensory room equipment meets international safety and educational standards?
Prioritize suppliers with ISO 9001 certification for quality management systems. Look for product-specific certifications such as EN71 (European toy safety), ASTM (American standards), or CE marking indicating compliance with EU regulations. For electrical or electronic sensory equipment, check for RoHS, FCC, or equivalent certifications. Confirm non-toxic, hypoallergenic, and fire-retardant material certifications, especially critical for school environments. Request copies of test reports and certification documents before finalizing orders. -
What are best practices for managing international shipping and logistics to ensure timely delivery of sensory room equipment?
Collaborate with suppliers experienced in exporting to your region to navigate customs and import documentation efficiently. Choose reliable freight forwarders familiar with your destination’s port or airport procedures. Clarify Incoterms (e.g., FOB, CIF, DDP) upfront to understand responsibility for shipping costs and risks. Plan for possible delays in customs clearance by factoring buffer time into your project schedule. Utilize tracking systems and maintain open communication channels with logistics partners to promptly address issues.
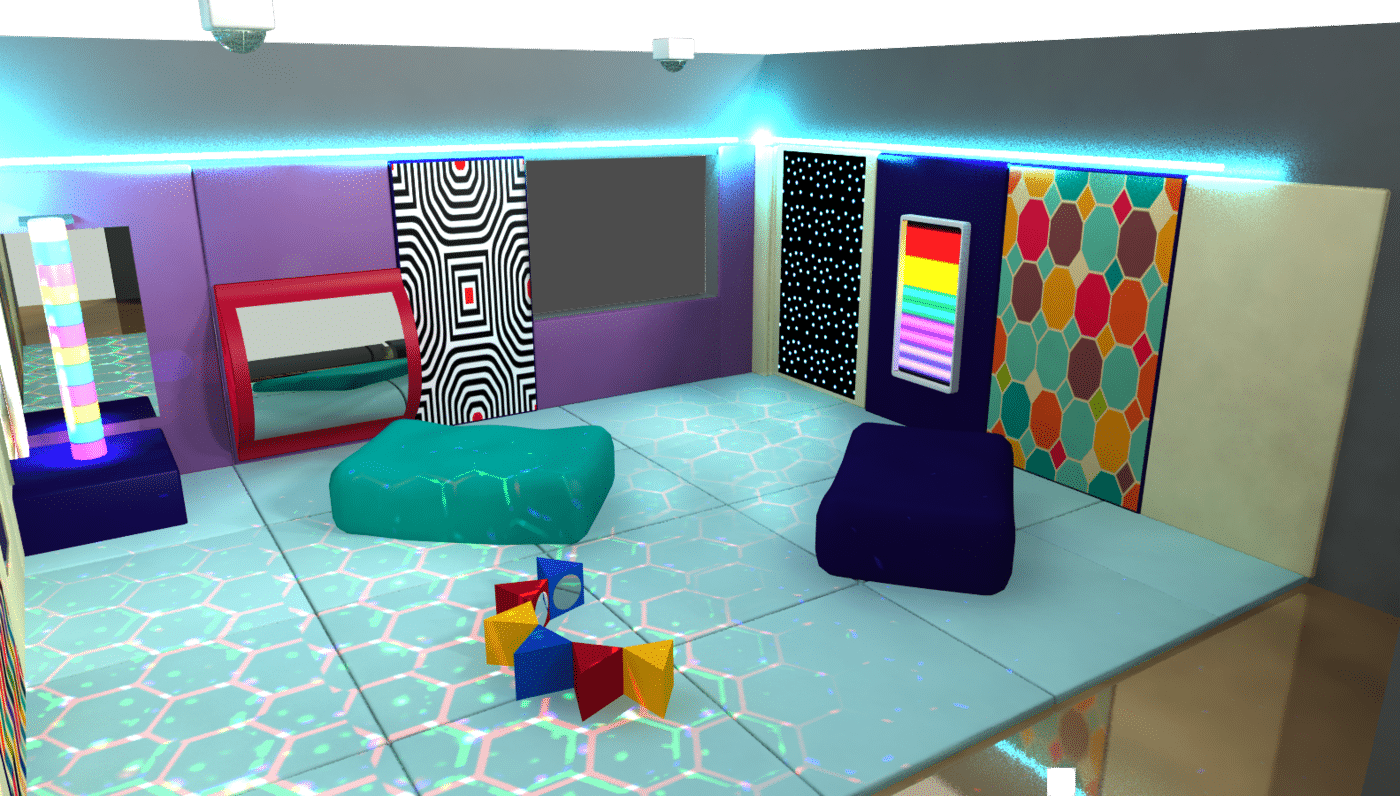
Illustrative Image (Source: Google Search)
-
How can I protect my purchase and resolve disputes if sensory room equipment does not meet agreed specifications or quality standards?
Include detailed product specifications and quality criteria in your purchase contract. Use third-party pre-shipment inspections to verify compliance before shipment. Opt for payment methods that offer buyer protection, such as Letters of Credit. In case of disputes, engage suppliers through clear, documented communication and negotiation. If unresolved, consider mediation or arbitration clauses specified in your contract, preferably under internationally recognized frameworks like ICC or UNCITRAL. Maintain records of all correspondence and inspection reports to support your claims. -
Are there specific considerations when importing sensory room equipment to countries in Africa, South America, the Middle East, or Europe?
Each region has unique import regulations, tariffs, and product standards. For example, some African countries require local certification or testing before customs clearance. South American markets may impose strict labeling and documentation requirements. Middle Eastern countries often have stringent electrical safety and halal compliance standards. European buyers must ensure CE marking and compliance with GDPR if collecting data via smart equipment. Engage local customs brokers and legal experts to navigate these complexities efficiently. -
What strategies can help optimize costs without compromising quality when sourcing sensory room equipment internationally?
Leverage consolidated shipments to reduce freight costs and customs fees by ordering multiple product lines together. Negotiate volume discounts and flexible MOQs with suppliers. Consider sourcing standard components locally to complement imported specialized items, reducing lead times and costs. Prioritize suppliers offering warranties and after-sales support to minimize long-term expenses. Lastly, build strategic partnerships with reliable manufacturers for continuous supply and potential co-development of cost-effective solutions tailored to your market needs.
Important Disclaimer & Terms of Use
⚠️ Important Disclaimer
The information provided in this guide, including content regarding manufacturers, technical specifications, and market analysis, is for informational and educational purposes only. It does not constitute professional procurement advice, financial advice, or legal advice.
While we have made every effort to ensure the accuracy and timeliness of the information, we are not responsible for any errors, omissions, or outdated information. Market conditions, company details, and technical standards are subject to change.
B2B buyers must conduct their own independent and thorough due diligence before making any purchasing decisions. This includes contacting suppliers directly, verifying certifications, requesting samples, and seeking professional consultation. The risk of relying on any information in this guide is borne solely by the reader.
Strategic Sourcing Conclusion and Outlook for sensory room equipment for schools
Strategic sourcing of sensory room equipment for schools requires a careful balance of quality, customization, and cost-efficiency. International B2B buyers should prioritize suppliers who offer versatile product ranges that cater to diverse sensory needs—ranging from calming aids to active sensory engagement tools. Understanding the specific requirements of end-users, such as students with developmental challenges, enables buyers to select equipment that maximizes therapeutic and educational outcomes. Additionally, evaluating supplier capabilities in terms of compliance with safety standards, delivery reliability, and after-sales support is critical for sustainable partnerships.
For buyers from Africa, South America, the Middle East, and Europe, leveraging regional trade networks and exploring manufacturers with proven export experience can reduce lead times and logistical complexities. Strategic sourcing also means investing in suppliers who provide scalable solutions adaptable to various school environments and budgets, ensuring long-term value and impact.
Looking ahead, the sensory room equipment market is poised for innovation, including the integration of technology-enhanced devices and customizable modular systems. International buyers are encouraged to stay informed on emerging trends and build relationships with forward-thinking suppliers to future-proof their sensory solutions. Embracing a strategic sourcing approach today not only enhances educational support for students worldwide but also positions buyers as leaders in inclusive learning environments.