Introduction: Navigating the Global Market for occupational room setup
Effective occupational room setup is a cornerstone for operational excellence in industries worldwide. For international B2B buyers—especially those navigating the diverse economic landscapes of Africa, South America, the Middle East, and Europe—understanding the nuances of occupational room configuration can unlock significant productivity gains and cost efficiencies. Whether outfitting manufacturing floors, maintenance storerooms, or specialized workspaces, the right setup directly influences workflow optimization, safety compliance, and asset longevity.
This comprehensive guide dives deeply into every critical facet of occupational room setup. You will explore a wide array of room types tailored to different industrial needs, from assembly and repair areas to storage and quality control zones. The guide examines essential materials and equipment specifications, emphasizing durability and regulatory standards that vary across regions. It also offers insights into manufacturing best practices and stringent quality control measures that ensure reliability and performance.
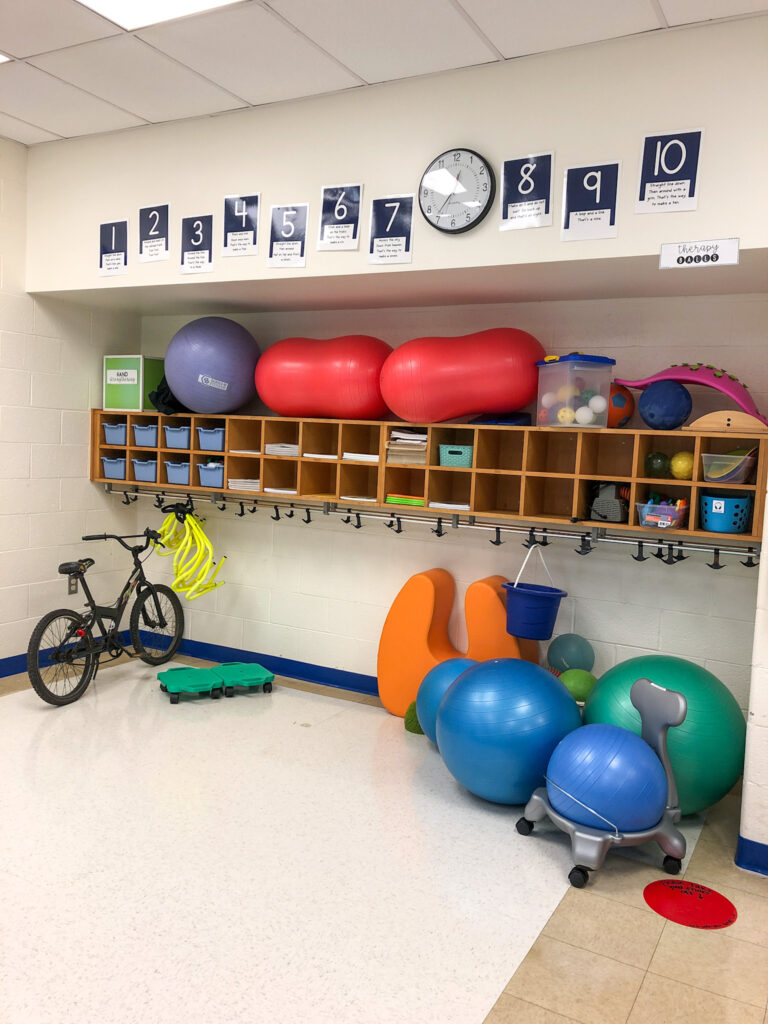
Illustrative Image (Source: Google Search)
For B2B buyers sourcing globally, the guide demystifies supplier selection, highlighting key considerations such as certification, lead times, and after-sales support. Cost factors are analyzed with a focus on balancing initial investment against long-term operational savings. Additionally, the guide provides a market overview, spotlighting trends and emerging technologies relevant to Africa, South America, the Middle East, and Europe—including dynamic markets like Turkey and Brazil.
Armed with this knowledge, international buyers can make informed, strategic decisions that align with their operational goals and regional requirements. This resource empowers you to optimize occupational room setups that drive efficiency, reduce downtime, and enhance overall business performance in a competitive global market.
Understanding occupational room setup Types and Variations
Type Name | Key Distinguishing Features | Primary B2B Applications | Brief Pros & Cons for Buyers |
---|---|---|---|
Manufacturing Storeroom Setup | Centralized parts storage, robust shelving, inventory tracking systems | Industrial manufacturing, maintenance & repair operations | Pros: Streamlines part retrieval, reduces downtime; Cons: Requires investment in technology and space |
Modular Office Setup | Flexible, reconfigurable furniture and partitions, technology integration | Corporate offices, consultancy firms, tech companies | Pros: Adaptable to changing team sizes; Cons: Higher initial cost, may require frequent adjustments |
Healthcare Room Setup | Sterile environment, specialized medical equipment, ergonomic design | Hospitals, clinics, diagnostic labs | Pros: Enhances patient safety and workflow; Cons: Strict regulatory compliance needed, costly equipment |
Retail Display Setup | Product-focused layout, customer flow optimization, attractive shelving | Retail stores, showrooms, wholesale outlets | Pros: Drives sales through visual merchandising; Cons: Requires frequent updates to match inventory and trends |
Remote/Hybrid Workspace Setup | Compact, tech-enabled workstations, soundproofing, connectivity solutions | Remote work hubs, co-working spaces, multinational corporations | Pros: Supports flexible work models; Cons: May need high investment in technology and infrastructure |
Manufacturing Storeroom Setup
This setup focuses on centralized storage for parts and tools essential for manufacturing and maintenance workflows. It emphasizes robust shelving, clear labeling, and advanced inventory management systems to reduce downtime caused by part shortages or misplacement. Ideal for companies in industrial sectors, buyers should prioritize storeroom technology that integrates with supply chain systems and consider space optimization to balance inventory levels and operational efficiency. For buyers in Africa or South America, investing in durable shelving and scalable inventory software can significantly improve maintenance turnaround times.
Modular Office Setup
Designed for dynamic work environments, modular office setups feature movable partitions and adaptable furniture to accommodate fluctuating team sizes and hybrid working models. This type is well-suited for corporate offices and tech companies in regions like Europe and the Middle East, where flexibility and technology integration are critical. Buyers should evaluate modularity ease, compatibility with existing IT infrastructure, and ergonomic standards to ensure productivity and employee comfort while managing costs.
Healthcare Room Setup
Healthcare occupational rooms require sterile, ergonomic designs equipped with specialized medical devices tailored to clinical workflows. These setups are vital for hospitals and diagnostic centers, especially in emerging markets where compliance with international health standards is becoming mandatory. B2B buyers must consider regulatory requirements, equipment certification, and supplier reliability to ensure patient safety and operational efficiency. The high initial investment is offset by improved care quality and workflow optimization.
Retail Display Setup
Retail setups prioritize customer engagement through strategic product placement, optimized traffic flow, and eye-catching displays. Showrooms and wholesale outlets benefit from layouts that enhance product visibility and ease of access. For buyers in regions like Turkey or Brazil, it’s essential to source adaptable shelving and fixtures that can be updated regularly to reflect changing inventory and consumer trends. The main challenge lies in balancing aesthetic appeal with durability and cost-effectiveness.
Remote/Hybrid Workspace Setup
This variation supports the growing trend of flexible work arrangements by providing compact, technology-enabled workstations with soundproofing and high-speed connectivity. Multinational corporations and co-working spaces across Europe and the Middle East are increasingly adopting this setup. Buyers should focus on integrating advanced communication tools, ergonomic furniture, and scalable infrastructure to support remote collaboration while maintaining data security and user comfort. The upfront technology investment is crucial for long-term workforce agility.
Related Video: Lecture 1 Two compartment models
Key Industrial Applications of occupational room setup
Industry/Sector | Specific Application of occupational room setup | Value/Benefit for the Business | Key Sourcing Considerations for this Application |
---|---|---|---|
Manufacturing | Maintenance, Repair, and Operations (MRO) storeroom organization | Reduces downtime by enabling rapid access to spare parts and tools | Durable shelving, modular storage units, and integration with inventory systems; local climate resilience for dust and humidity in regions like Middle East and Africa |
Healthcare | Sterile supply rooms and equipment storage | Ensures compliance with hygiene standards and speeds up medical workflows | Cleanroom-compatible materials, ergonomic design for quick access, and compliance with international health standards; sourcing from suppliers with certifications recognized in Europe and South America |
Automotive Industry | Parts and tool storage in assembly and repair workshops | Improves efficiency in assembly lines and reduces production stoppages | Heavy-duty racks, secure storage for high-value components, and flexibility for varied part sizes; consideration of import regulations and local supplier support in Turkey and Brazil |
Pharmaceuticals | Controlled environment rooms for sensitive materials and equipment | Maintains product integrity and regulatory compliance | Climate control systems, contamination control, and validated storage solutions; sourcing reliable HVAC and monitoring equipment suited for humid tropical climates in South America and Africa |
Electronics Manufacturing | Cleanroom and ESD-safe occupational rooms | Protects sensitive components from static and contamination | ESD-compliant flooring and furniture, controlled airflow systems, and modular layouts; emphasis on suppliers with experience in ESD and cleanroom standards for European and Middle Eastern markets |
Manufacturing: MRO Storeroom Organization
In manufacturing plants, occupational room setups primarily focus on organizing MRO storerooms to ensure that critical spare parts and tools are easily accessible. This setup minimizes unplanned downtime by facilitating rapid maintenance and repair. Buyers from Africa, South America, the Middle East, and Europe should prioritize sourcing durable, modular storage solutions that withstand local environmental challenges such as dust and humidity. Integration with inventory management technology is essential to maintain accurate stock levels and prevent stockouts, which are costly in fast-paced production environments.
Healthcare: Sterile Supply Rooms
Hospitals and clinics rely on occupational room setups that maintain sterile environments for medical supplies and equipment. These rooms must meet strict hygiene and ergonomic standards to support efficient medical workflows and patient safety. International buyers should source materials and designs compliant with global health regulations, ensuring that storage solutions are easy to clean and maintain. Certifications recognized in Europe and South America can facilitate regulatory approvals and adoption in local healthcare facilities.
Automotive Industry: Parts and Tool Storage
Automotive assembly and repair workshops benefit significantly from occupational rooms designed for organized parts and tool storage. Such setups streamline assembly processes and reduce production halts caused by missing components. Buyers in Turkey, Brazil, and other regions should look for heavy-duty racks and secure storage options that accommodate diverse part sizes and protect valuable components. Additionally, understanding local import regulations and supplier service capabilities is critical to ensure timely delivery and support.
Pharmaceuticals: Controlled Environment Rooms
Pharmaceutical companies require occupational rooms with strict environmental controls to store sensitive materials and equipment. These rooms prevent contamination and ensure compliance with regulatory standards. Sourcing climate control and contamination management systems suitable for tropical and arid climates—common in South America and Africa—is vital. Buyers should also seek validated storage solutions and reliable HVAC systems that maintain consistent temperature and humidity levels, safeguarding product integrity.
Electronics Manufacturing: Cleanroom and ESD-safe Rooms
In electronics manufacturing, occupational rooms must protect sensitive components from electrostatic discharge (ESD) and particulate contamination. This necessitates specialized flooring, furniture, and controlled airflow systems. Buyers targeting European and Middle Eastern markets should emphasize suppliers experienced in ESD and cleanroom standards, ensuring compliance and operational efficiency. Modular room layouts can provide flexibility for evolving production needs and facilitate maintenance activities without compromising environmental controls.
Related Video: Industrial Control Panel Basics
Strategic Material Selection Guide for occupational room setup
Analysis of Common Materials for Occupational Room Setup
1. Stainless Steel
Key Properties: Stainless steel offers excellent corrosion resistance, high strength, and good temperature tolerance, typically up to 870°C for some grades. It is non-porous and hygienic, making it ideal for environments requiring cleanliness and durability.
Pros & Cons: Its durability and resistance to chemical exposure make it a top choice for occupational rooms, especially where moisture or corrosive agents are present. However, stainless steel can be costly and heavier than alternatives, with fabrication requiring specialized equipment and skills.
Impact on Application: Stainless steel is suitable for equipment surfaces, storage units, and fixtures that demand hygiene and longevity. It resists staining and microbial growth, critical for medical or laboratory occupational rooms.
International Considerations: Buyers from Africa, South America, the Middle East, and Europe should verify compliance with ASTM A240 or EN 10088 standards, which are widely recognized. In regions like Turkey and Brazil, local certifications might also apply. The higher upfront cost is often justified by reduced maintenance and longer lifecycle.
2. Powder-Coated Steel
Key Properties: Powder-coated steel combines the strength of steel with a protective polymer coating that enhances corrosion resistance and aesthetic appeal. It performs well under moderate temperature ranges and offers good impact resistance.
Pros & Cons: This material is more cost-effective than stainless steel and easier to manufacture and customize. However, the coating can chip or scratch, exposing the steel underneath to corrosion, especially in humid or saline environments.
Impact on Application: Ideal for shelving, racks, and cabinets in occupational rooms where moderate durability and cost-efficiency are priorities. It suits dry or controlled environments but may require touch-ups or recoating in harsher climates.
International Considerations: Compliance with ISO 12944 for corrosion protection and ASTM D3359 for coating adhesion is important. Regions with high humidity or coastal exposure, such as parts of South America and the Middle East, should consider enhanced coating specifications or alternative materials.
3. High-Density Polyethylene (HDPE)
Key Properties: HDPE is a thermoplastic known for its chemical resistance, impact strength, and moisture impermeability. It performs well in a wide temperature range (-50°C to 80°C) and is lightweight.
Pros & Cons: HDPE is cost-effective, easy to fabricate, and resistant to many chemicals, making it suitable for surfaces and containers. However, it is less heat-resistant than metals and can deform under prolonged high temperatures or heavy mechanical stress.
Impact on Application: Commonly used for storage bins, work surfaces, and protective panels in occupational rooms where chemical exposure is a concern but heavy structural strength is not critical.
International Considerations: Buyers should ensure compliance with FDA or EU food-grade standards if the setup involves food or pharmaceuticals. In Africa and South America, cost-effectiveness and ease of transport favor HDPE, but UV stabilization may be necessary in sunny climates.
4. Aluminum
Key Properties: Aluminum is lightweight, corrosion-resistant, and has good thermal conductivity. It withstands moderate temperatures and is easily machinable.
Pros & Cons: Aluminum offers a good balance between strength and weight, making it easier to handle and install than steel. However, it is softer and more prone to surface scratches and dents. Its cost is generally higher than powder-coated steel but lower than stainless steel.
Impact on Application: Suitable for frames, panels, and lightweight furniture in occupational rooms where mobility and corrosion resistance are important but extreme durability is not required.
International Considerations: Compliance with ASTM B209 or EN AW standards is common. Aluminum’s recyclability is a plus for European buyers focused on sustainability. In Middle Eastern and African markets, anodized aluminum is preferred for enhanced corrosion resistance.
Summary Table of Materials for Occupational Room Setup
Material | Typical Use Case for occupational room setup | Key Advantage | Key Disadvantage/Limitation | Relative Cost (Low/Med/High) |
---|---|---|---|---|
Stainless Steel | Equipment surfaces, storage units, fixtures | Superior corrosion resistance and hygiene | High cost and fabrication complexity | High |
Powder-Coated Steel | Shelving, racks, cabinets | Cost-effective with good corrosion protection | Coating can chip, exposing steel to corrosion | Medium |
High-Density Polyethylene (HDPE) | Storage bins, work surfaces, protective panels | Chemical resistance and lightweight | Lower heat resistance and structural strength | Low |
Aluminum | Frames, panels, lightweight furniture | Lightweight and corrosion-resistant | Softer, prone to scratches and dents | Medium |
In-depth Look: Manufacturing Processes and Quality Assurance for occupational room setup
Manufacturing Processes for Occupational Room Setup
Occupational room setups, which typically include modular furniture, ergonomic fixtures, safety installations, and specialized equipment, require a multi-stage manufacturing process to ensure functionality, durability, and compliance with workplace standards. Understanding these stages is essential for B2B buyers to evaluate potential suppliers effectively.
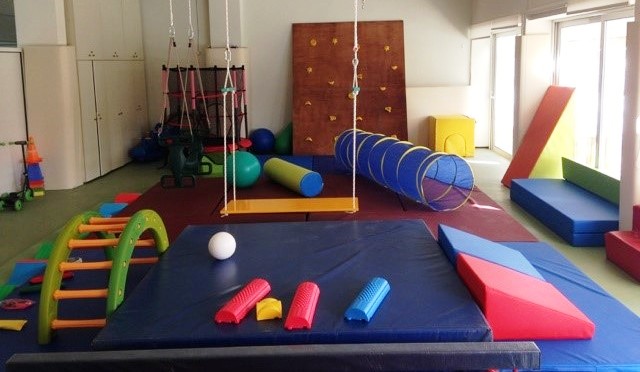
Illustrative Image (Source: Google Search)
1. Material Preparation
The manufacturing journey begins with sourcing and preparing raw materials such as steel, aluminum, high-grade plastics, laminates, and upholstery fabrics. Materials must meet predefined specifications regarding strength, fire resistance, and chemical safety. For example, metals may undergo cutting, deburring, and surface treatment (e.g., galvanizing or powder coating) to prevent corrosion and improve longevity in occupational environments.
2. Forming and Fabrication
This stage involves shaping materials into components through methods like stamping, bending, welding, and injection molding. Advanced CNC machining and laser cutting are increasingly used for precision and repeatability. Ergonomic design considerations are integrated here to meet workplace safety and comfort standards, ensuring components like adjustable desks and seating conform to user requirements.
3. Assembly
Component parts are systematically assembled, often combining mechanical fasteners, adhesives, or welding depending on product design. This stage may involve modular assembly lines tailored for customization, enabling clients to specify configurations for their occupational rooms. Integration of electrical systems (lighting, outlets, sensors) also occurs here, requiring coordination between mechanical and electrical manufacturing teams.
4. Finishing and Surface Treatment
Final finishing enhances both aesthetics and durability. Common techniques include powder coating, painting, laminating, and upholstery work. Finishing processes are critical for occupational environments where hygiene, chemical resistance, and ease of cleaning are vital. Quality finishes also contribute to long-term wear resistance and compliance with occupational health and safety regulations.
Quality Assurance Frameworks and Checkpoints
Quality assurance (QA) in occupational room setup manufacturing is a rigorous, multi-tiered process designed to ensure products meet international standards and client-specific requirements. B2B buyers should prioritize suppliers who implement comprehensive QA systems aligned with global best practices.
International Quality Standards
- ISO 9001: The cornerstone for quality management systems (QMS), ISO 9001 certification ensures that a manufacturer maintains consistent quality in processes and outputs. It emphasizes continual improvement and customer satisfaction.
- CE Marking: Particularly relevant for European buyers, the CE mark indicates conformity with health, safety, and environmental protection standards for products sold within the European Economic Area.
- Industry-Specific Certifications: Depending on the occupational room’s use, certifications like API (American Petroleum Institute) standards or ANSI (American National Standards Institute) may apply, especially if the setup includes specialized industrial or safety equipment.
Key Quality Control (QC) Checkpoints
- Incoming Quality Control (IQC): Raw materials and components undergo verification for specifications, defects, and compliance before entering production.
- In-Process Quality Control (IPQC): Continuous inspection during forming, assembly, and finishing stages ensures early detection of defects, dimensional accuracy, and adherence to design specifications.
- Final Quality Control (FQC): The finished product is evaluated against functional, safety, and aesthetic criteria. This includes visual inspections, mechanical testing, and performance validation.
Common Testing Methods
B2B buyers should look for suppliers employing robust testing protocols, including:
- Material Testing: Tensile strength, hardness, corrosion resistance, and fire retardancy tests validate raw materials’ suitability for occupational environments.
- Dimensional and Functional Testing: Precision gauges, coordinate measuring machines (CMM), and functional simulations verify that components fit correctly and operate as intended.
- Load and Ergonomic Testing: Furniture and fixtures undergo load-bearing tests to confirm structural integrity and ergonomic assessments to ensure user comfort and safety.
- Environmental and Chemical Resistance Testing: Exposure to humidity, chemicals, and cleaning agents simulates workplace conditions to guarantee product durability.
Verifying Supplier Quality Control: Practical Steps for B2B Buyers
For international buyers, especially in Africa, South America, the Middle East, and Europe, verifying supplier QC is critical for mitigating risks and ensuring product reliability.
- On-site Audits: Conduct or commission factory audits to assess manufacturing capabilities, process controls, and compliance with international standards. Audits provide direct insight into supplier operations and quality culture.
- Review of Quality Documentation: Request ISO certificates, inspection reports, material test certificates, and process control documents. These demonstrate the supplier’s adherence to quality frameworks.
- Third-Party Inspections: Engage independent inspection agencies to perform pre-shipment inspections, random sampling, and testing. This is particularly valuable for buyers unable to visit supplier sites frequently.
- Sample Testing: Evaluate product samples in your local market or third-party labs to verify material properties, dimensions, and functional performance before placing large orders.
Quality Assurance Nuances for International B2B Buyers
Regional Compliance Considerations
- Africa and South America: Buyers should note variability in local regulatory enforcement and may require suppliers to provide enhanced documentation and third-party certifications to meet import and occupational safety standards.
- Middle East: Compliance with GCC (Gulf Cooperation Council) standards and adherence to regional safety and fire codes may be mandatory. Suppliers familiar with these can better navigate customs and certification processes.
- Europe (including Turkey): Strict adherence to CE marking and EU Directives (e.g., REACH for chemical safety) is essential. Buyers should verify that suppliers maintain updated certifications reflecting evolving EU regulations.
Logistics and Documentation
International buyers must ensure clear communication regarding quality expectations and documentation requirements upfront. Differences in terminology, standards interpretation, and testing methods can lead to misunderstandings; hence, specifying detailed quality agreements and acceptance criteria in contracts is vital.
Conclusion
For B2B buyers investing in occupational room setups, understanding the manufacturing process and quality assurance mechanisms is fundamental to securing high-quality, compliant products. By focusing on supplier certifications, QC checkpoints, rigorous testing, and verification methods, buyers from Africa, South America, the Middle East, and Europe can mitigate risks and ensure their occupational environments are safe, ergonomic, and durable. Strategic supplier selection combined with proactive quality management ultimately drives operational efficiency and workplace safety.
Related Video: Amazing factories | Manufacturing method and top 4 processes | Mass production process
Comprehensive Cost and Pricing Analysis for occupational room setup Sourcing
When sourcing occupational room setups, understanding the intricate cost structure and pricing factors is vital for international B2B buyers aiming to optimize investment and operational efficiency. The pricing of such setups encompasses multiple layers of costs and market influences, each requiring thorough consideration.
Key Cost Components
Materials: The choice of raw materials—ranging from ergonomic furniture, specialized lighting, to electronic fittings—significantly impacts costs. Premium or certified materials (e.g., antimicrobial surfaces) elevate expenses but may offer long-term value through durability and compliance.
Labor: Skilled labor for manufacturing, assembly, and installation is a major cost driver. Labor costs vary widely by region, with emerging markets often offering competitive rates but requiring attention to quality standards.
Manufacturing Overhead: Includes factory utilities, equipment depreciation, and indirect labor. Efficient production management and lean manufacturing practices can reduce overhead, influencing final pricing.
Tooling and Customization: Custom molds, specialized fixtures, or bespoke design elements increase upfront tooling costs. These are amortized over order volumes but can significantly affect unit costs for small to medium orders.
Quality Control (QC): Rigorous QC processes ensure compliance with occupational health and safety standards. This may involve third-party certifications, testing, and audits, adding to the total cost but safeguarding product reliability.
Logistics and Freight: International shipping costs, customs duties, and handling fees vary by destination. For buyers in Africa, South America, the Middle East, and Europe, logistics costs can fluctuate substantially due to port infrastructure and import regulations.
Supplier Margin: Supplier pricing includes a margin to cover business risk, financing, and profit. Negotiation and volume commitments can influence this margin.
Influencers of Pricing
Volume and Minimum Order Quantity (MOQ): Larger orders usually benefit from economies of scale, reducing per-unit costs. Small or custom orders may incur premium pricing due to setup costs and less efficient production runs.
Specifications and Customization: Tailoring room setups to specific occupational needs—such as adjustable workstations or integrated technology—raises costs. Buyers should balance customization benefits against budget constraints.
Material Quality and Certifications: Products with international certifications (e.g., ISO, CE, ANSI) or eco-friendly credentials command higher prices but enhance market acceptance and compliance.
Supplier Reputation and Location: Established suppliers with proven quality records may charge premiums but reduce risk. Proximity to manufacturing hubs can lower logistics costs and lead times.
Incoterms: Shipping terms (e.g., FOB, CIF, DDP) determine the cost responsibility split between buyer and seller, affecting total landed cost. Buyers must evaluate which terms align best with their logistics capabilities.
Practical Buyer Tips for International B2B Procurement
Negotiate Beyond Price: Engage suppliers on payment terms, warranty, after-sales support, and volume discounts. For buyers in emerging markets like Turkey or Brazil, building long-term partnerships can unlock favorable terms.
Focus on Total Cost of Ownership (TCO): Consider installation, maintenance, energy consumption, and potential downtime costs alongside purchase price. Investing in higher-quality components may reduce lifecycle expenses.
Understand Pricing Nuances by Region: Import duties, taxes, and compliance requirements differ across Africa, South America, the Middle East, and Europe. Early consultation with customs brokers and local experts can prevent unexpected costs.
Leverage Technology for Transparency: Use digital procurement platforms and inventory management tools to track orders, monitor pricing trends, and optimize reorder points, reducing excess inventory and storage costs.
Validate Supplier Capabilities: Request samples, certifications, and client references. For critical occupational setups, third-party audits or factory visits (virtual or physical) ensure adherence to quality and safety standards.
Disclaimer on Pricing
All cost indications are subject to change based on market dynamics, currency fluctuations, supplier negotiations, and specific project requirements. Buyers should treat price estimates as indicative and conduct detailed quotations and feasibility analyses before finalizing procurement decisions.
By adopting a holistic approach to cost and pricing analysis, international B2B buyers can secure occupational room setups that balance quality, compliance, and cost-efficiency, ultimately supporting safer and more productive work environments across diverse regions.
Spotlight on Potential occupational room setup Manufacturers and Suppliers
This section looks at several manufacturers active in the ‘occupational room setup’ market. This is a representative sample for illustrative purposes; B2B buyers must conduct extensive due diligence before any transaction. Information is synthesized from public sources and general industry knowledge.
Modular Operation Theatres
Nine Sunplus Systems (NSS) specializes in designing and manufacturing modular systems for operation theatres, intensive care units, recovery rooms, and hospital wards. With over 15 years of experience, NSS delivers tailor-made modular cladding and prefabricated partition solutions that optimize space and maintain strict bacterial control, catering to global healthcare providers.
- 🌐 Domain: nsmot.com
- 📅 Creation Year: 2017
- ⏳ Registered For: ~8.3 years
Operating room
Operating room suppliers offer modular, integrated solutions designed to enhance efficiency and flexibility in surgical environments. Their product range includes customizable operating theaters with advanced medical device integration, telemedicine capabilities, and streamlined cleaning processes. These solutions target healthcare facilities globally, supporting optimized workflows and cost-effective operating room management.
- 🌐 Domain: medicalexpo.com
- 📅 Creation Year: 1997
- ⏳ Registered For: ~28.3 years
10 Operating Room Management Companies
Operating room management companies specialize in optimizing surgical workflows, resource allocation, and equipment readiness to enhance patient safety and operational efficiency. Their solutions often include surgical scheduling, staff coordination, and data-driven performance monitoring. These firms serve hospitals and healthcare providers worldwide, focusing on cost reduction and improved surgical outcomes across diverse international markets.
- 🌐 Domain: globalgrowthinsights.com
- 📅 Creation Year: 2023
- ⏳ Registered For: ~2.0 years
Essential Technical Properties and Trade Terminology for occupational room setup
Critical Technical Properties for Occupational Room Setup
When sourcing occupational room setup solutions, understanding key technical properties ensures compatibility, durability, and compliance with operational needs. Here are essential specifications to evaluate:
Material Grade and Composition
The quality of materials (e.g., steel grade, wood type, or composite makeup) directly impacts durability, safety, and maintenance frequency. For example, stainless steel with a corrosion-resistant grade is vital in humid or chemically sensitive environments common in manufacturing or healthcare. Buyers should confirm material certifications to match local standards and usage conditions.Dimensional Tolerance
This defines allowable deviations in size and fit of components such as shelving units, partitions, or fixtures. Tight tolerances guarantee proper assembly and function, reducing installation delays and costly adjustments. In B2B contracts, specifying tolerance levels avoids disputes and ensures interoperability with existing infrastructure.Load Capacity and Weight Limits
Shelving, racks, and storage units must support expected loads without compromising safety. This includes static weight (stored items) and dynamic weight (movement during handling). Accurate load ratings help prevent accidents, equipment damage, and downtime, particularly crucial in industrial setups with heavy machinery or bulk storage.Fire and Safety Compliance
Occupational rooms must adhere to fire resistance, smoke emission, and safety codes specific to regions (e.g., Europe’s EN standards, Middle East fire codes). Materials and finishes should be certified for flame retardancy and non-toxicity. Buyers should request compliance documentation to ensure legal conformity and workplace safety.Environmental Resistance
Depending on geographic and operational factors (humidity, temperature, dust), components may require resistance to corrosion, UV exposure, or chemical spills. Selecting products with appropriate coatings or finishes extends lifespan and reduces maintenance costs, especially for buyers in tropical climates or industrial zones.Modularity and Scalability
Systems designed with modular components allow easier upgrades, expansions, and reconfigurations, supporting evolving operational needs. This flexibility can reduce long-term costs and downtime, an important consideration for companies planning growth or frequent layout changes.
Key Trade Terminology for International B2B Buyers
Navigating occupational room setup procurement involves understanding common trade terms that clarify responsibilities, pricing, and order requirements:
OEM (Original Equipment Manufacturer)
Refers to the company that produces the original parts or equipment. Buying OEM products ensures authenticity, quality, and compatibility. For occupational rooms, OEM-supplied fixtures or components often come with better warranties and service support.MOQ (Minimum Order Quantity)
The smallest quantity a supplier is willing to sell. MOQ affects pricing and inventory planning. Buyers from emerging markets should negotiate MOQs aligned with their budget and storage capacity to avoid excess stock or cash flow issues.RFQ (Request for Quotation)
A formal process where buyers ask suppliers to provide pricing, lead times, and terms for specified products or services. Well-prepared RFQs with detailed technical requirements help buyers receive accurate, comparable offers, accelerating decision-making.Incoterms (International Commercial Terms)
Standardized trade terms defining the responsibilities and risk transfer points between buyer and seller during shipping (e.g., FOB, CIF, DDP). Understanding Incoterms is critical for budgeting logistics costs and ensuring compliance with import regulations in regions like Africa and South America.Lead Time
The period between order placement and delivery. Accurate lead time information allows buyers to plan project timelines, avoid stockouts, and coordinate installation schedules. Longer lead times may require advance ordering or interim solutions.Bill of Materials (BOM)
A comprehensive list detailing all parts and materials needed for a setup or assembly. A clear BOM facilitates accurate sourcing, budgeting, and quality control. Buyers should request or provide detailed BOMs to suppliers to minimize errors and streamline procurement.
Understanding these technical properties and trade terms empowers international B2B buyers to make informed decisions, negotiate effectively, and ensure occupational room setups meet operational and regulatory demands across diverse markets.
Navigating Market Dynamics, Sourcing Trends, and Sustainability in the occupational room setup Sector
Market Overview & Key Trends
The occupational room setup sector is increasingly influenced by globalization, technological innovation, and shifting workplace norms. For B2B buyers in Africa, South America, the Middle East, and Europe—including emerging markets such as Turkey and Brazil—understanding these dynamics is crucial for sourcing competitive, functional, and scalable solutions.
Global Drivers:
The rise of hybrid work models and enhanced focus on employee well-being have propelled demand for ergonomic, flexible occupational environments. Organizations seek modular furniture, smart storage solutions, and integrated digital technologies that improve space utilization and operational efficiency. Additionally, rapid urbanization and industrial growth in regions like Africa and South America are stimulating investments in modern occupational infrastructure, creating new sourcing opportunities.
Key Market Dynamics:
– Customization and Modularity: Buyers prioritize setups that can be tailored to diverse work styles and easily reconfigured to meet evolving organizational needs, reducing total cost of ownership.
– Technology Integration: Smart room setups incorporate IoT sensors, automated inventory management, and AI-driven space optimization, enabling predictive maintenance and real-time monitoring.
– Local vs. Global Sourcing: While global manufacturers offer cutting-edge solutions, local suppliers in regions such as the Middle East and Turkey provide competitive pricing and faster lead times, important for projects with tight deadlines.
– Supply Chain Resilience: Recent disruptions have heightened the focus on diversified sourcing strategies, including multi-vendor partnerships and nearshoring to reduce risks and logistical costs.
Emerging Sourcing Trends:
– Adoption of digital procurement platforms enhances transparency and supplier collaboration.
– Growing preference for vendors offering end-to-end services, from design consultation to installation and after-sales support.
– Increasing demand for standardized components that comply with international safety and quality certifications, facilitating cross-border compliance.
Sustainability & Ethical Sourcing in B2B
Sustainability has become a non-negotiable factor in occupational room setup procurement, driven by regulatory pressures and corporate social responsibility commitments. B2B buyers must integrate environmental and ethical considerations into their sourcing decisions to future-proof investments and align with stakeholder expectations.
Environmental Impact:
Materials used in occupational setups—such as wood, metals, plastics, and textiles—can have significant ecological footprints. Prioritizing low-impact materials like FSC-certified wood, recycled metals, and biodegradable or recyclable composites helps minimize deforestation, mining damage, and landfill waste. Efficient design that maximizes space and durability reduces the need for frequent replacements, cutting resource consumption over time.
Ethical Supply Chains:
Transparency in labor practices and sourcing origins is essential to avoid reputational risks associated with forced labor, unsafe working conditions, or unfair wages. Buyers should insist on suppliers who demonstrate compliance with international labor standards and ethical trade certifications such as SA8000 or Fair Trade.
Green Certifications & Standards:
– LEED (Leadership in Energy and Environmental Design): Ensures products contribute to sustainable building certifications.
– BIFMA LEVEL: A certification specific to furniture sustainability, addressing material health, energy use, and social responsibility.
– Cradle to Cradle: Focuses on circular economy principles, encouraging reuse and recyclability of materials.
By incorporating these sustainability criteria, B2B buyers in diverse regions can reduce operational risks, improve brand equity, and meet increasingly stringent environmental regulations.
Brief Evolution of Occupational Room Setup
The occupational room setup has evolved significantly from traditional, static office layouts to dynamic, technology-enabled environments. Initially focused on basic furniture provision, the sector expanded in the late 20th century to include ergonomic designs responding to workplace health concerns. The 2000s ushered in open-plan offices and collaborative spaces, emphasizing flexibility.
More recently, digital transformation and the COVID-19 pandemic accelerated the adoption of hybrid work models, necessitating modular, tech-integrated setups that support remote collaboration and wellness. This evolution underscores the sector’s shift from purely functional design to holistic, adaptive environments aligned with organizational agility and employee experience—key considerations for B2B buyers evaluating long-term occupational space investments globally.
Related Video: Incoterms for beginners | Global Trade Explained
Frequently Asked Questions (FAQs) for B2B Buyers of occupational room setup
How can I effectively vet suppliers for occupational room setup products across different regions such as Africa, South America, and Europe?
To vet suppliers internationally, start by verifying their business licenses, certifications, and references from existing clients, especially within your region. Use platforms like Alibaba, Global Sources, or regional trade directories, and request product samples to assess quality firsthand. Conduct virtual or on-site audits if possible, focusing on their manufacturing capabilities, quality control processes, and compliance with international standards. Pay attention to suppliers’ experience with export regulations and their ability to handle customs documentation, which is crucial for smooth cross-border transactions.What level of customization is typically available for occupational room setups, and how should I communicate my specific needs to suppliers?
Most reputable suppliers offer customization options ranging from layout design, furniture dimensions, materials, to ergonomic features tailored to occupational needs. Clearly define your requirements using detailed specifications, CAD drawings, or photos, and discuss compliance with local occupational health and safety standards. Providing use-case scenarios and expected workflow can help suppliers recommend optimal solutions. Always confirm customization capabilities early in negotiations to avoid delays and ensure the final setup aligns with your operational goals.What are common minimum order quantities (MOQ), lead times, and payment terms for international orders of occupational room setups?
MOQs vary widely depending on the supplier and product complexity but typically range from small batch orders (10-50 units) to larger commitments (100+ units) for custom setups. Lead times can span 4-12 weeks, factoring in design, production, and shipping. Payment terms often include a 30%-50% deposit upfront with the balance due upon delivery or before shipment. Negotiate terms to include milestones or partial payments aligned with production stages to minimize risk. Request clear timelines and consider buffer periods for customs clearance.Which quality assurance (QA) certifications and standards should I require from occupational room setup suppliers?
Demand suppliers hold ISO 9001 certification for quality management systems as a baseline. For occupational environments, certifications like ISO 45001 (occupational health and safety), CE marking (for European markets), and compliance with ANSI/BIFMA standards (for office furniture safety and durability) are critical. Verify third-party inspection reports and ask for sample testing results. Insist on documented QA processes and factory inspection opportunities to ensure consistent product quality, especially when sourcing from emerging markets.What logistical challenges should I anticipate when importing occupational room setups to regions like Africa, the Middle East, or South America?
Common challenges include complex customs procedures, variable port infrastructure, and potential delays due to local holidays or political instability. Packaging must protect products during long transit and multiple handling stages. Collaborate with freight forwarders experienced in your target region to optimize shipping routes and modes (sea, air, or multimodal). Plan for additional clearance documentation such as certificates of origin, import licenses, and compliance declarations. Understanding local import duties and taxes upfront helps avoid unexpected costs.
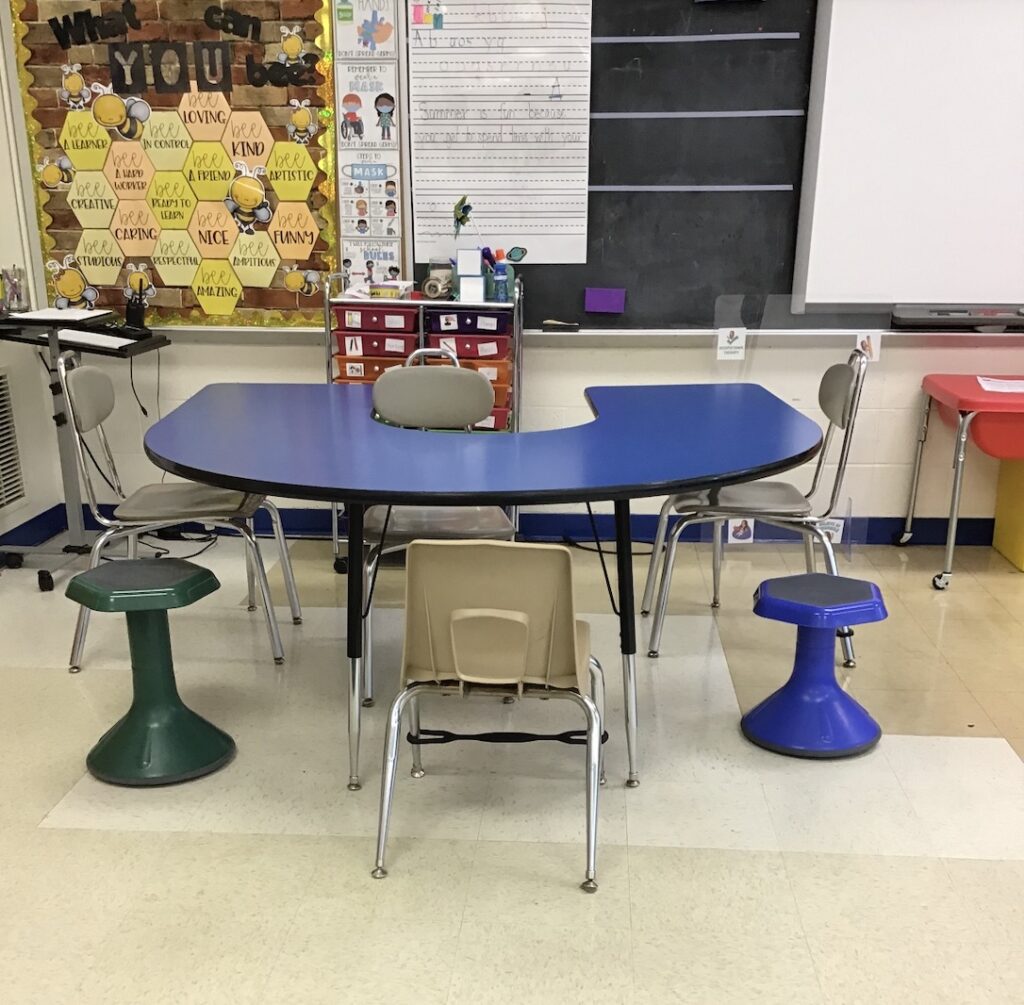
Illustrative Image (Source: Google Search)
How can I mitigate risks of disputes related to product quality or delivery delays in international occupational room setup contracts?
Draft clear contracts specifying product specifications, delivery schedules, payment terms, and penalties for non-compliance. Include inspection rights before shipment and require suppliers to provide pre-shipment photos or third-party inspection certificates. Use incoterms like FOB or CIF to clarify responsibilities and risks during transit. Maintain open communication channels and document all interactions. Consider using escrow payment services or letters of credit to protect financial interests. Establish dispute resolution mechanisms, preferably through arbitration in a neutral jurisdiction.Are there specific considerations for occupational room setups to comply with local regulations in diverse markets such as Turkey or Brazil?
Yes, each country may have unique building codes, ergonomic standards, fire safety regulations, and environmental requirements. For example, Brazil emphasizes ABNT standards for furniture safety, while Turkey requires compliance with TÜV certifications and local labor laws. Engage local consultants or legal experts to review designs and materials for compliance. Ensure suppliers understand these requirements and can provide necessary documentation. Adapting setups to local cultural preferences and climate conditions also enhances user acceptance and durability.What payment methods are safest and most efficient for international transactions in occupational room setup sourcing?
Bank wire transfers (T/T) remain common but carry risks if the supplier is unverified. Letters of credit (L/C) offer strong protection by tying payment to document compliance but involve higher costs and complexity. Escrow services provide a middle ground by holding funds until contract terms are met. For smaller or initial orders, using trade assurance platforms can enhance security. Always verify banking details independently and avoid advance payments without confirmed contracts. Align payment terms with delivery milestones to balance cash flow and risk.
Important Disclaimer & Terms of Use
⚠️ Important Disclaimer
The information provided in this guide, including content regarding manufacturers, technical specifications, and market analysis, is for informational and educational purposes only. It does not constitute professional procurement advice, financial advice, or legal advice.
While we have made every effort to ensure the accuracy and timeliness of the information, we are not responsible for any errors, omissions, or outdated information. Market conditions, company details, and technical standards are subject to change.
B2B buyers must conduct their own independent and thorough due diligence before making any purchasing decisions. This includes contacting suppliers directly, verifying certifications, requesting samples, and seeking professional consultation. The risk of relying on any information in this guide is borne solely by the reader.
Strategic Sourcing Conclusion and Outlook for occupational room setup
Effective occupational room setup hinges on strategic sourcing that aligns equipment, storage solutions, and workflow design with operational priorities. For international B2B buyers—especially in emerging and diverse markets across Africa, South America, the Middle East, and Europe—leveraging localized supplier expertise combined with global best practices ensures optimal cost-efficiency, compliance, and scalability. Prioritizing vendor reliability, inventory accuracy, and modular storage systems can dramatically reduce downtime and enhance productivity.
Key takeaways for buyers include:
– Optimizing space and inventory management to minimize waste and maximize operational flow.
– Investing in durable, adaptable storage infrastructure that supports quick access and maintenance efficiency.
– Implementing clear labeling and part classification systems to streamline replenishment and reduce stockouts.
– Partnering with suppliers who understand regional logistics and compliance nuances, enabling smoother procurement and delivery cycles.
Looking ahead, occupational room setups will increasingly integrate smart inventory technologies and sustainable materials, supporting both environmental goals and cost controls. Buyers are encouraged to adopt a proactive sourcing strategy that anticipates future operational demands and embraces innovation. By doing so, companies across these regions can build resilient, efficient occupational environments that drive long-term competitive advantage.